High Quality Rigid-Flex Circuit Boards for Your Application Needs
By:admin
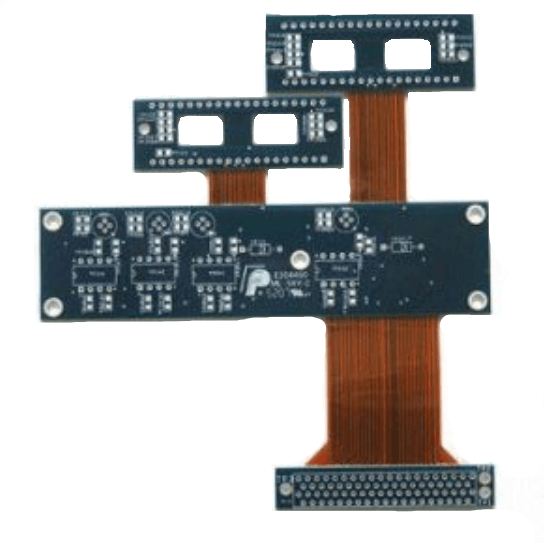
At MCL, we are dedicated to meeting the diverse needs of our clients, and that is why we have developed the Rigid-Flex PCB. The circuit board combines the strengths of both rigid and flexible PCBs, which creates a unique design that is useful in multiple applications.
Our rigid-flex circuits are complex, but our specialized team of engineers is up to the task. We use state-of-the-art equipment and methodologies to ensure that our product is of the highest quality and to guarantee that your applications run efficiently.
The key reasons why clients should consider using MCL's Rigid-Flex Circuits include its light-weight, space-saving design, and the freedom with which this design allows hardware to be manipulated. Moreover, our technology has the capability to withstand the high-stress, vibration, and shock that often cause PCB failure in harsh environments.
With our Rigid-Flex Circuits, clients have the option to choose from a variety of materials, finishes, thicknesses, and production volumes. This flexibility makes it possible for our clients to obtain a custom PCB that suits their unique requirements.
We ensure that our rigid-flex circuits are designed with the latest fabrication techniques that guarantee durability, reliability, and accuracy, while also accommodating trace width and vias.
MCL's experienced team of PCB engineers and technicians easily adapt to the changing needs of clients and the market. We use our design expertise to optimize the strength and flexibility of our boards while keeping the PCB dimensions to a minimum.
At MCL, we use the most advanced, cost-effective technologies that ensure our PCBs stand up to the most rigorous environments. We strive to deliver our PCBs promptly and without any compromise on quality.
Our Rigid-Flex Circuits are highly versatile and can be used in a variety of applications, such as medical devices, aerospace technology, automobile electronics, and portable gadgets. Our team collaborates with our clients to design PCBs that match their applications' needs and meet their specifications.
In summary, Rigid-Flex Circuits offered by MCL is an efficient, safe, and cost-effective technology for producing high-quality PCBs that meet industry standards and exceed the expectations of our clients. Our team of highly skilled professionals and state-of-the-art technologies can produce custom designs that meet even the most complex requirements of our clients.
As a leading manufacturer and supplier of PCBs, we are confident in our abilities to produce high-quality products that enable our clients to succeed. For Rigid-Flex Circuitboards, MCL sets the trend and leads the way in innovation. Contact us today if you need an efficient and reliable supplier of Rigid-Flex Circuit boards.
Company News & Blog
How to correctly solder earphone wires to a connector board
Wiring, Earphone Connector Board, Soldering, Audio ConnectivityAre you tired of your earphones getting tangled or giving you connectivity issues? The solution to this problem lies in the proper soldering of the earphone wires in the connector (circuit) board.Soldering is a process in which two or more metal items are joined together by melting and then cooling a filler metal into the joint, forming a reliable, electrically conductive and mechanically strong connection. Soldering requires skill and precision, but with a little bit of practice, it can be done correctly.The first step to correctly soldering your earphone wires is to prepare the connector board. Use a wire cutter to trim the wires to the desired length, and then strip off the insulation at the end of each wire to expose the bare metal. Next, carefully insert each wire into the appropriate hole in the connector board, being sure to match the colors of the wires to the corresponding color-coded holes.Once the wires are in place, it's time to solder them. Use a soldering iron to heat the metal contact points of the circuit board and the bare wire ends of each earphone wire. Apply a small amount of solder wire to the joint, ensuring that it melts well and flows smoothly into the joint.It's important to note that overheating the wires or applying too much heat to the metal contact points can damage the circuit board, which could result in poor connectivity or even total failure.It's also a good idea to perform a continuity test on each wire after soldering, using a multimeter to ensure that the connections are properly made and that there is no interruption in the signal flow.Properly soldering your earphone wires in the connector board can make a significant difference in the audio quality and connectivity of your earphones. Remember to exercise caution and be patient, and with a little bit of practice, you'll be able to achieve perfect soldering every time.In conclusion, soldering earphone wires to the connector board is an essential step in ensuring proper audio connectivity. Whether you're installing a new circuit board or repairing an existing one, the process requires precision and care. Properly soldering the wires can greatly improve the sound quality of your headphones, ensuring years of perfect audio performance.
PCBA Testing Services - Comprehensive Quality Checks for Your Electronics
With the fast development of technology, electronic devices have become an indispensable part of our daily lives. From smartphones to smart homes, every device is built with the smallest yet the most complex printed circuit board (PCB) assembled with various electronic components. However, the quality of PCB assembly is paramount to the performance and lifespan of devices. As a professional electronic assembly service provider, we at FASTBOM understand the importance of reliable PCB assembly. That's why we provide our clients with rigorous testing procedures to ensure the quality of our products. Our testing process includes PCBA testing, X-ray testing, functional testing, and final visual inspection. First of all, we conduct PCBA testing to examine the soldering joints of each component. This step is especially essential for Ball Grid Array (BGA) package components. Due to its complex structure, soldering BGA requires higher standards. We use professional machines to check the inner solder problems of BGA packages to ensure that every unit meets our strict quality standards. Afterward, we perform X-ray testing for customers who use BGA package ICs in their design. Our X-ray machine provides all-encompassing solder joint inspection without jeopardizing the integrity of the PCB assembly. With this test, we can further ensure that the soldering joint performed meets the requirements of the assembly process. If the above tests are passed, we move on to the functional test, which we do free of charge for our customers. We provide a free functional test jig as well as programming burning that is compatible with your design. The testing method is usually offered by customers, but if a customer can’t provide this information, our engineer will design a test method for the board. The last step in our testing process is the final visual inspection. We use a magnifying glass to ensure the placement and direction of every component, as well as the quality of the soldering joints. Our QC department checks every unit before we clean the board to ensure that the product is ready to ship. As we mentioned above, we are FASTBOM, a platform owned by MOKO Technology Ltd. We provide reliable electronic assembly services to customers from all over the world. We have been in the industry for over ten years and have long been trusted by our clients to provide high-quality PCB assembly services promptly. In conclusion, electronic devices are an essential part of our daily lives, and having a reliable PCB assembly can ensure the performance and longevity of your device. With our strict quality testing procedures, you can rely on us to deliver a reliable and high-quality electronic assembly service. Trust us at FASTBOM to be your partner in providing the best quality PCB assembly for your electronic devices. Keywords: PCB assembly testing, BGA package, functional testing, visual inspection.
Latest developments in PCB industry: Breaking news and expert opinions
The Printed Circuit Board (PCB) industry has been rapidly growing over the recent years. A PCB is an essential component of electronic devices, which serves as a platform for electronic components to be connected to each other. It provides the required electrical connections, thereby ensuring the functioning of electronic devices. PCBs are used in numerous electronic products, including computers, mobile phones, televisions, and automotive electronics, among others.The demand for PCBs has been increasing due to the growth of the electronic industry and the Internet of Things (IoT) devices. The IoT devices are expected to bring in a new wave of demand, as they would require advanced and highly sophisticated PCBs. Increasing investment in 5G technology is expected to further fuel the demand for advanced PCBs.The PCB industry has been witnessing several trends, including technological advancements, demand for eco-friendly PCBs, increasing automation, and the shift towards the use of flexible and rigid-flex PCBs. Technological advancements have made PCBs smaller, lighter, and more efficient, thereby improving the performance and functionality of electronic devices. The demand for eco-friendly PCBs has been increasing due to the growing awareness regarding environmental issues.The PCB industry has been dominated by a few players, with the majority of the market share held by Chinese and Taiwanese companies. However, the industry has been witnessing new players entering the market, such as Indian companies, which are expected to be a key growth driver in the future.One such company that has been making a mark in the Indian PCB industry is {company name}. The company was established in {year}, and has since been providing high-quality PCBs to numerous customers across the globe. The company boasts of a state-of-the-art manufacturing facility, which is equipped with the latest machinery and equipment. The company specializes in manufacturing single-sided, double-sided, and multi-layer PCBs. The company’s products cater to various industries, including automotive, telecommunications, consumer electronics, and medical, among others.{Company name} has been focusing on innovation and technological advancements, which has helped it differentiate itself from the competition. The company has been developing advanced PCBs, such as high-speed PCBs, flexible and rigid-flex PCBs, and metal core PCBs, among others. The company’s advanced products have been well-received by customers, and have helped it establish a strong foothold in the market.Another area that {company name} has been focusing on is sustainability. The company has been using eco-friendly materials and processes for manufacturing PCBs, thereby reducing its environmental impact. The company has also been focusing on reducing waste and recycling materials, thereby promoting a circular economy.{Company name} has been expanding its operations, with plans to set up a new manufacturing facility in {location} to cater to the growing demand for PCBs. The new facility is expected to be equipped with the latest machinery and equipment, and will be a green facility, which would further the company’s commitment towards sustainability.The PCB industry is expected to continue to grow, driven by the growth of the electronic industry and the increasing demand for advanced PCBs. {Company name} is well-positioned to capitalize on this growth, and has been gaining recognition as a leading PCB manufacturer in the region. With its focus on innovation, sustainability, and customer satisfaction, {company name} is poised for growth and success in the years to come.
Tips for Fast and Effective Circuit Board Prototyping
Outsourcing, Prototype Circuit Board, PCB Manufacturing, PCB Assembly, Circuit Board DesignPrototype circuit board outsourcing is the process of a company contracting with a PCB manufacturer to build a prototype circuit board based on a design. This is an important step in the development of electronic products because it allows the designer to test the function of the circuit board before committing to large scale production. In addition, the designer can use the prototype to identify any issues that might arise during the manufacturing process.One of the main benefits of outsourcing the production of a prototype circuit board is speed. Quick turn circuit boards can be manufactured in as little as 24 hours, allowing designers to test their designs without delay. This is particularly important in rapidly changing industries where time-to-market is critical.Another benefit of outsourcing the production of a prototype circuit board is cost. Many PCB manufacturers offer competitive pricing for quick turn prototypes, allowing designers to test their designs without committing large amounts of capital.When outsourcing the production of a prototype circuit board, it is important to find a manufacturer with experience in PCB manufacturing and assembly. The manufacturer should have the ability to handle complex designs, including multi-layer boards, high density interconnects and surface mount components.In addition to experience, the manufacturer should also have a quality management system in place to ensure that the prototype is manufactured to the required specifications. This includes a process for identifying and addressing any issues that arise during the manufacturing process.In summary, outsourcing the production of a prototype circuit board is an important step in the development of electronic products. Quick turn circuit boards offer speed and cost benefits and allow designers to test their designs in a timely and cost-effective manner. When selecting a manufacturer, it is important to consider their experience and quality management system to ensure a successful outcome.
In response to the need for improved protection of flexible circuits, a new method of double-sided soldermask application is becoming increasingly popular. Liquid photoimageable soldermask is now replacing older methods. To accommodate this change, technological advancements were necessary, leading to the development of the Smart Print System for coating and handling extremely thin flexible circuits.
: Meet the Demand for Double-Sided SoldermaskFlexible circuits have become increasingly popular in recent years due to their numerous benefits such as being lightweight, flexible, and easy to integrate into various products. They are widely used in industries such as aerospace, medical devices, consumer electronics and more. However, with more complex applications, the need for improved circuit protection has become paramount. This is where the double-sided soldermask comes in. What is Double-Sided Soldermask?Soldermask is a coating applied to the copper traces and pads on a printed circuit board (PCB). It is designed to protect the circuit during the assembly process and prevent unintended solder contacts. Traditionally, soldermask was applied to only one side of a PCB. However, with the growing demand for flexible circuits, the industry now requires double-sided soldermask, which is an insulating, protective coating applied to both sides of the flexible circuit.Why the Need for Double-Sided Soldermask?Double-sided soldermask is necessary for flexible circuits because these circuits are often bent, twisted, and shaped to fit into a variety of devices. As a result, the delicate circuits need protection not only on one side but on both sides to ensure their longevity. Without this added protection, the longevity and quality of the circuit may be compromised - and no one wants that. Advantages and Disadvantages of Double-Sided SoldermaskAdvantages:- Increased protection: Double-sided soldermask offers more comprehensive protection to flexible circuits, making them more durable and less prone to damage.- Enhanced performance: The protective coating can help to improve the electrical properties of the circuit and reduce the possibility of interference.- Flexibility: With the added protection, flexible circuits can be bent and manipulated with less risk of damage.Disadvantages: - More complex manufacturing: Double-sided soldermask adds an extra layer of complexity to the manufacturing process, driving up production costs and increasing the time required to complete the circuit.- More technical challenges: Applying the coating to both sides of the circuit can be tricky, especially when dealing with thin and flexible circuits.- Limited Availability: Not all manufacturers are equipped with the technology and knowledge to produce double-sided soldermask circuits.How Circuit Automation is Meeting the Demand?To meet the demand for double-sided soldermask, Circuit Automation developed and commercialized the DP3500 coater. This technology is specifically designed to handle and coat very thin flexible circuits, overcoming the technical challenges associated with this application. The liquid photoimageable soldermask technology used in the DP3500 coater enables the production of circuits with double-sided soldermask, providing better protection and long-lasting performance.The DP3500 coater is also equipped with the Smart Print System (SPS), which is a proprietary technology that ensures accurate and consistent coating thickness, even on delicate flexible circuits. The SPS allows for precision printing of the soldermask on both sides of the circuit, minimizing errors and improving the overall quality of the finished product. ConclusionIn summary, the demand for double-sided soldermask has been driven by the need for improved protection and durability of flexible circuits. While this technology adds complexity to the manufacturing process, it also offers significant benefits and helps to improve the overall performance of the circuit. Circuit Automation has answered the call by developing the DP3500 coater and the Smart Print System, making double-sided soldermask circuits accessible and affordable for a wide range of industries.
Transforming the Manufacturing of Electrical and Electronic Appliances with 4 Layer PCBs
Printed Circuit Boards (PCBs) have revolutionized the manufacturing of electrical and electronic appliances, and 4 Layer PCB is no exception. These multi-layered PCBs have gained immense popularity over the years due to their versatility and efficiency in circuit design and layout.4 Layer PCBs are a type of multi-layered circuit board that consists of four electrically conductive layers separated by insulating layers. The four conductive layers of the 4 Layer PCB allow for the creation of complex circuit designs that are not possible with single or double-layered PCBs. They offer superior signal integrity and feature high-density interconnects, making them ideal for use in high-speed digital applications.In recent times, 4 Layer PCBs have become a popular choice for many industries, including aerospace, military, telecommunications, and consumer electronics. The demand for these PCBs has surged due to their ability to handle high-frequency signals, low power consumption, high reliability, and reduced manufacturing costs.The Benefits of Using 4 Layer PCB4 Layer PCBs offer several benefits over single- or double-layered PCBs. Some of the benefits include:1. Increased Density: With more conductive layers, 4 Layer PCBs offer greater density which means that the circuitry can be made more complex. This allows for more electrical components to be placed on the board without compromising on their functionality.2. Reduced Size: The increase in density makes it possible to create smaller and lighter PCBs, which can lead to cost savings and greater flexibility in design.3. Improved Signal Integrity: The four layers of the PCB allow for better signal performance, reduced noise, and less interference from other electronic components.4. Enhanced Thermal Performance: The extra layers of the PCB provide better heat dissipation, resulting in improved thermal performance for electronic devices.5. Cost Savings: The use of 4 Layer PCBs results in significant cost savings as they reduce the material and manufacturing costs associated with producing complex circuit designs.The Use of Any Layer PCBAny Layer PCB is another type of multi-layered PCB that can be used as a substitute for 4 Layer PCBs due to its versatility. As the name suggests, Any Layer PCB offers total flexibility to design engineers as to the number of layers they can use. Unlike other PCBs, Any Layer PCBs do not have any limitations in terms of the number of layers they have.The use of Any Layer PCB has become an increasingly popular choice in modern-day electronic devices due to its features. These PCBs offer a minimalist approach to circuit board design, which leads to a reduction in weight, size, and cost. Furthermore, the layer stacking system is implemented using alternating layers of PCB materials, resins, and copper-traces that reduce the overall wastage of copper, making them more environmentally friendly.ConclusionThe use of 4 Layer PCBs and Any Layer PCBs has transformed the electronics industry by offering superior performance and cost-efficient solutions. These PCBs have become essential components in the manufacture of various devices like smartphones, televisions, and medical equipment. The benefits of using 4 Layer PCBs and Any Layer PCBs include increased density, reduced size, improved signal integrity, enhanced thermal performance, and cost savings. As technology continues to advance, it is clear that the use of multi-layered PCBs will become more common, and the demand for them will continue to rise.
In-House Circuit Card Assembly Capabilities at Battelle
Building and Testing Circuit Card Assembly BoardsCircuit Card Assembly Testing is an essential requirement for ensuring the quality and reliability of electronic devices. From consumer electronics to industrial controls, virtually all electronic devices rely on robust and reliable circuit boards to function properly. A Circuit Card Assembly (CCA) Board is a key component in any electronic device, and it is essential that the assembly process and testing procedures are done correctly for optimal performance.A Circuit Card Assembly Board is a complex and intricate system that requires precision manufacturing techniques to build, assemble, and test. A CCA Board is composed of several electronic components, including resistors, capacitors, diodes, transistors, and integrated circuits, among other things. Each component plays a vital role in the overall functionality and reliability of the board.The Build ProcessBuilding a Circuit Card Assembly Board requires a set of standard procedures and significant technical expertise. The assembly process starts with the design of the board and identifying the electronic components that will be required to build the board. The board must be optimized with a design that meets the necessary electrical, thermal, and mechanical requirements.Once the design is finalized, the schematic design is converted into a layout that can be used for manufacturing. The layout of the board is used to create a stencil that is used to place the electronic components precisely. The stencil ensures that each component is placed correctly to avoid any shorts or misplacing of electronic components.Once the board's stencil is created, the board is manufactured by carefully placing each electronic component on the board, using automated machines and careful manual labor. The components are then assembled using solder paste that allows the components to adhere to the board and provides electrical contact.Testing the Circuit Card Assembly BoardWith the board successfully assembled, the next and most crucial step is testing the Circuit Card Assembly Board. Testing ensures that the board functions correctly, meets the specifications, and is free from defects.The testing process involves several steps, and it is highly dependent on the type of board and its intended use. The common types of testing include:- Visual Inspection: A Visual Inspection is performed to ensure that there are no visible defects, including bent pins, missing components, or shorts.- Functional testing: Function testing is carried out to verify that the board functions correctly. It involves applying power to the board and checking that each electronic component is working correctly. Functional testing can be automated or done manually, depending on the complexity of the board.- Environmental testing: Environmental testing simulates the operating environment of the board and is done to ensure that the board can operate correctly in harsh conditions. Environmental testing includes temperature cycling, vibration testing, and shock testing.- Burn-in Testing: Burn-in testing is carried out to verify the reliability of the board. The Board is subjected to long term stress testing to identify any defects that may not be noticeable during initial testing.In-house CapabilityManufacturing and testing Circuit Card Assembly Boards require a high level of technical expertise, experience, and sophisticated equipment. Circuit Card Assembly Board builds or circuit card assemblies (CCA) are a crucial in-house capability that any electronic device manufacturer should possess. Battelle (remove the brand name) has invested heavily in Equipment, personnel, and training to ensure that they have the capability to build and test CCA boards.In conclusion, Circuit Card Assembly Testing is a critical aspect of ensuring the quality and reliability of electronic devices. Building and Testing Circuit Card Assembly Boards require the right equipment, expertise, and a highly trained workforce. Circuit Card Assembly Board builds or circuit card assemblies (CCA) are a crucial in-house capability that any electronic device manufacturer should possess. If you're looking for a reliable and experienced company to build and manufacture CCA boards, look no further than Battelle's Electronics and Manufacturing Services Division.
Get Rapid Prototyping and Fast Delivery for PCBs with Quick Turn Services
: The Importance of Timely DeliveryIn today's fast-paced world, where technological advancements are happening at an unprecedented rate, Quick Turn Printed Circuit Boards (PCBs) have emerged as a game-changer. These PCBs are capable of speeding up the production process and helping businesses meet their deadlines. With a growing demand for PCBs, it has become imperative for manufacturers to deliver them on time to remain competitive in the market.In this blog post, we will discuss the importance of timely delivery of Quick Turn PCBs and why it is critical for businesses to choose a reliable and trusted supplier for their PCB needs.Meeting DeadlinesDeadlines are crucial for businesses, and delays in delivery can result in significant losses both in terms of time and money. PCBs are an essential component in many industries, including automotive, medical, aerospace, and telecommunications, among others. Ensuring timely delivery of these PCBs can be the difference between meeting customer expectations and losing business to competitors. Therefore, choosing a supplier who can deliver custom-made PCBs quickly and efficiently is fundamental.Reducing CostsManufacturers can incur additional costs if the PCBs are not delivered on time. For example, if the delivery of PCBs is delayed, the company might need to switch to air freight, which can be expensive. Additionally, any missed deadlines or late deliveries can lead to production downtime, staff overtime payments, and a loss of revenue. Therefore, timely delivery of Quick Turn Printed Circuit Boards can help businesses save costs and stay competitive in the market.Maintaining Quality StandardsQuick Turn PCBs are designed and manufactured at a rapid pace. Therefore, it is essential to ensure that the quality of these PCBs is not compromised in the process. A reliable and trustworthy supplier will guarantee that the PCBs meet industry standards and quality requirements, ensuring customer satisfaction. This ultimately leads to repeat business and more significant opportunities for growth and expansion.Choosing the Right SupplierChoosing the right PCB supplier is crucial to ensure timely delivery of Quick Turn PCBs. A reliable and quality supplier will have a streamlined production process in place, ensuring faster delivery times. They will also employ highly skilled and experienced personnel to manufacture Printed Circuit Boards and perform quality control checks to ensure the PCBs meet industry standards.ConclusionIn today's ever-changing and demanding marketplace, timely delivery of Quick Turn Printed Circuit Boards is crucial for businesses to meet customer expectations and stay ahead of the competition. Therefore, it is essential to choose a reliable supplier who can guarantee on-time delivery, maintain quality standards, and provide cost-effective solutions for your PCB needs.At WonderfulPCB, we are committed to providing exceptional services to our clients by delivering Quick Turn PCBs within a short duration and ensuring quality standards are met. Contact us today for all your PCB requirements, and we will be happy to help you meet your deadlines and ensure business success.
Diverse Circuit Board Suppliers Offer Solutions for Multiple Industries - Find Top-Quality PCBs Now
Circuit Board Suppliers Provide Options for Many Industries: Are You Looking for the Best Manufactured Printed Circuit Boards?In today's technological world, printed circuit boards (PCBs) are essential components in almost all electronic devices. From smartphones and computers to transportation systems and medical devices, PCBs play a critical role in making our modern lives possible.Given the importance of PCBs, it's crucial to find the right circuit board supplier for your industry's needs. Fortunately, there are many options available, and with the rise of flexible PCB circuit board technology, the possibilities are nearly limitless.What are Printed Circuit Boards?First, let's define what PCBs are and how they work. A PCB is a board made of a non-conductive material (usually fiberglass or plastic) that is covered in thin copper layer inside. PCBs are designed to connect multiple electronic components, such as resistors, capacitors, and transistors, into a single functional unit.The circuit patterns on a PCB are created by etching the copper layer. Components are then added to complete the circuit, and the board is coated with solder to make the connections between components. The end result is a compact, reliable circuit board that can be mass-produced at low cost.Why are PCBs important?PCBs have revolutionized the world of electronics by simplifying the manufacturing of complex circuits, reducing the size of electronic devices, and increasing their reliability. PCBs are essential components in many life-critical applications, such as medical devices and transportation systems, where electrical failure could have disastrous consequences.What are Flexible PCB Circuit Boards?Traditional PCBs are made of rigid materials like fiberglass or plastic. However, in recent years, the rise of flexible PCB technology has allowed the circuits to be printed onto flexible materials like polyester or polyimide. This flexible material is then coated with conductive materials to create the circuit board.Flexible PCBs have many advantages over traditional PCBs, including:1. Flexibility: Flexible PCBs can be bent or folded to conform to the shape of the device, making them ideal for use in wearable electronics or curved displays.2. Light weight: Because they are made of a thin, flexible material, flexible PCBs weigh less than traditional PCBs.3. Cost-effective: The manufacturing process for flexible PCBs is more efficient, with less waste and lower production costs.4. Reliable: Flexible PCBs are more resilient to shocks and vibrations than traditional PCBs.5. Space-saving: Flexible PCBs can be designed to fit into tight spaces where traditional PCBs couldn't fit, making them ideal for small, portable devices.Choosing the Right Circuit Board SupplierWhen it comes to choosing the right circuit board supplier, there are several key factors to consider:1. Quality: Make sure that your supplier uses high-quality materials and components in their PCBs.2. Flexibility: If you require flexible PCBs, make sure that your supplier has experience with this technology.3. Capability: Choose a supplier that has the capability to produce PCBs in the quantity you require.4. Cost: While you want to find the most cost-effective solution, don't sacrifice quality for cost.5. Lead times and delivery: Make sure that your supplier can deliver your PCBs on time, in the quantities you need.ConclusionWhether you need traditional PCBs or flexible PCBs, it's important to choose the right circuit board supplier for your industry's specific needs. With the right supplier, you can be confident that your PCBs will meet your expectations for quality, flexibility, and reliability. So, make sure to research and choose the right supplier that can provide you with the best manufactured printed circuit boards.
Latest Stock Quote, History, and News for an Electronic Manufacturing Services Company
Flex Ltd.: A Leader in Electronic Manufacturing ServicesFlex Ltd. is a global electronics manufacturing services (EMS) company based in Singapore. Founded in 1969, the company is a leading provider of design, engineering, and manufacturing services to a wide range of industries, including automotive, healthcare, industrial, and communication. The company has over 200,000 employees and operates in 30 countries around the world.One of the key strengths of Flex is its ability to offer end-to-end EMS solutions that help customers bring innovative products to market faster and more cost-effectively. The company's comprehensive services include design and engineering, manufacturing, supply chain management, and after-sales support. This allows customers to focus on their core competencies, while Flex takes care of the rest.Flex has proven expertise in a broad range of technologies, including Internet of Things (IoT), 5G wireless, artificial intelligence, and robotics. The company's ability to integrate these technologies into its EMS offerings allows it to provide customers with cutting-edge solutions that drive innovation and accelerate growth.Recent NewsFlex has recently been in the news for several reasons. In March 2021, the company announced that it had won a contract to manufacture medical devices for Flow, a UK-based medical technology company. Under the agreement, Flex will manufacture Flow's handheld device, which is used to treat asthma and chronic obstructive pulmonary disease (COPD). This contract demonstrates Flex's expertise in the healthcare industry and its commitment to partnering with customers to develop innovative and life-changing products.In addition, Flex has been actively involved in the fight against COVID-19. The company has ramped up production of critical medical supplies, such as ventilators, oxygen concentrators, and personal protective equipment (PPE), to help meet the global demand for these products. Flex has also been working with customers to develop new medical devices and technologies that can help diagnose and treat COVID-19.Financial PerformanceFlex has a strong track record of financial performance. In its most recent fiscal year (ended March 31, 2020), the company reported revenue of $24.2 billion, up 4% from the previous year. Net income was $243 million, or $0.45 per share.Despite the challenges posed by the COVID-19 pandemic, Flex has continued to deliver strong financial results. In its most recent quarter (ended December 31, 2020), the company reported revenue of $6.7 billion, up 3% from the same period a year earlier. Net income was $173 million, or $0.32 per share.Flex's strong financial performance has been driven by several factors, including its diverse customer base, its focus on innovation and operational excellence, and its commitment to sustainability. The company has a robust balance sheet, with a net debt position of $1.2 billion, and a strong liquidity position, with cash and cash equivalents of $2.5 billion as of December 31, 2020.Investment PotentialFlex's strong financial performance, combined with its leadership position in the EMS industry, make it an attractive investment opportunity for investors. The company's stock (NYSE:FLEX) has performed well over the past year, with a total return of over 50%. As of March 26, 2021, the stock was trading at $18.67 per share, with a market capitalization of $9.9 billion.Analysts have a positive outlook for Flex's future performance. According to Yahoo Finance, the consensus rating for the stock is a "buy," with an average target price of $20.11 per share. This represents a potential upside of over 7% from the current market price.ConclusionFlex Ltd. is a leading provider of electronic manufacturing services, with a proven track record of innovation, operational excellence, and financial performance. The company's end-to-end solutions, expertise in cutting-edge technologies, and commitment to sustainability make it an attractive investment opportunity for investors. With a strong balance sheet and a diverse customer base, Flex is well-positioned to continue delivering value to its stakeholders and driving growth in the EMS industry.