Explore Flexible PCB Solutions for Your Circuit Board Needs on icape-shop.com
By:admin
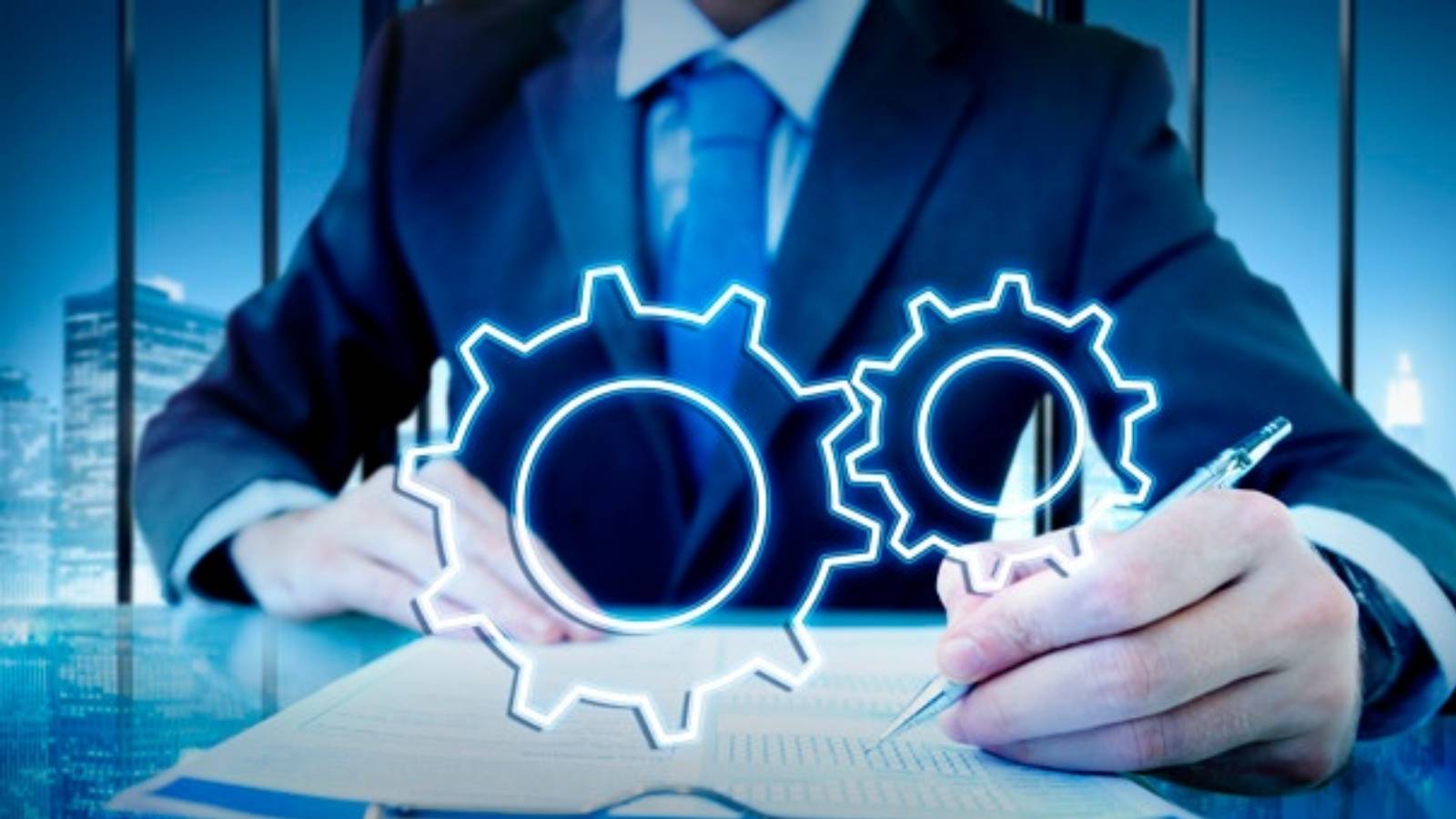
The world of electronics is constantly evolving, with new technology and innovations emerging all the time. One of the most exciting developments in recent years has been the rise of rigid-flex printed circuit boards (PCBs). These PCBs are a hybrid of both rigid and flexible PCB technologies, allowing for more flexible designs and greater functionality in electronic devices.
As one of the leading providers of printed circuit board solutions, the ICAPE Group is at the forefront of the rigid-flex PCB revolution. With a wide range of cutting-edge solutions for flexible PCBs, ICAPE is helping companies across a range of industries take advantage of this powerful technology.
Whether you're looking to create a highly complex electronic device or a simple, streamlined product, flexible PCBs can provide the design versatility and functionality you need. With flexible PCBs, the circuits are mounted on top of a flexible substrate, rather than a rigid board. This allows the PCB to bend and flex, which can be particularly useful in applications where space is limited or where the board may be subjected to high levels of vibration or other stresses.
One of the key benefits of flexible PCBs is their ability to improve reliability and reduce failure rates. Because they can be designed to fit the exact needs of a particular application, they can also be more reliable over the long term. Additionally, because they can be constructed with fewer parts than traditional PCBs, they are often less prone to failure.
At ICAPE, we offer a range of solutions for flexible PCBs that can be customized to meet the specific needs of your application. Our expert engineers can work closely with you to develop a design that meets your exact requirements, ensuring that you get the best possible results.
Our flexible PCBs are available in a range of materials, including copper, polyester, and thermoplastics. We can also provide a range of different levels of flexibility, making it possible to create a PCB that can bend and flex to a high degree or one that is more rigid and stable.
In addition to our flexible PCB solutions, we also offer a range of other printed circuit board solutions to suit your needs. These include standard and complex multilayer PCBs, as well as specialized boards for high-frequency applications and more.
At ICAPE, our focus is on providing our customers with the highest quality printed circuit board solutions that can help them succeed in a rapidly changing and highly competitive market. Whether you're looking for flexible PCBs, rigid PCBs, or any other type of PCB solution, we have the expertise and experience needed to deliver the results you need.
If you're interested in learning more about our flexible PCB solutions, please visit our e-shop at www.icape-shop.com. We would be happy to answer any questions you may have and help you find the perfect solution for your needs.
Company News & Blog
High Density PCB Layout of DC/DC Converters: Reducing Converter Losses for Compact Space-Constrained Applications
[Company Name] Continues to Innovate with High-Density PCB Layout for DC/DC Converters[City, State]—As the demand for compact, space-constrained applications continues to rise, [Company Name], a leading provider of cutting-edge power management solutions, is proud to introduce their latest innovation in high-density PCB layout for DC/DC converters. This breakthrough technology allows system designers to optimize power management in a smaller footprint, contributing to overall efficiency and performance.Power management is a critical aspect of any electronic system, and the dedicated area on a printed circuit board (PCB) for such components is often limited. Developers face the challenge of reducing converter losses while maintaining compactness. Addressing these challenges head-on, [Company Name] has invested significant research and development efforts into their latest high-density PCB layout solutions, delivering unrivaled performance and design flexibility.The new high-density PCB layout for DC/DC converters from [Company Name] enables system designers to achieve substantial space savings without compromising efficiency or performance. By utilizing advanced semiconductor technologies and innovative design techniques, [Company Name] has successfully reduced power losses and improved overall thermal management. This allows for a compact realization, ideal for applications where space is a critical constraint.One of the key advantages of [Company Name]'s high-density PCB layout is its ability to significantly reduce power losses. By carefully optimizing the layout and incorporating advanced power management circuitry, [Company Name] has achieved remarkable efficiency levels. This not only enhances performance but also contributes to the overall system reliability. With reduced power losses, the new layout solution enables applications to operate more efficiently while consuming lower levels of power, leading to cost savings and extended battery life.In addition to reducing power losses, [Company Name]'s high-density PCB layout solution excels in thermal management. As electronic systems become more compact, managing heat dissipation becomes increasingly challenging. However, with the integration of advanced thermal management techniques, [Company Name] has successfully enhanced the performance and reliability of their DC/DC converters. By efficiently dissipating heat away from critical components, their high-density PCB layout ensures stable operation even in demanding environments.The compactness achieved through [Company Name]'s high-density PCB layout opens up a world of possibilities for system designers, allowing them to create innovative designs in space-constrained applications. Whether it be in portable consumer electronics, industrial automation systems, or automotive applications, the reduced size and improved power management capabilities of [Company Name]'s solution provide immense flexibility for developers.Furthermore, [Company Name] fully supports the integration of their high-density PCB layout solution into a wide range of applications. With their comprehensive technical support and customer service, system designers can confidently implement this innovative solution into their designs, ensuring optimal performance and reliability.[Company Name] has a long-standing reputation for delivering high-quality power management solutions, and their latest high-density PCB layout for DC/DC converters further solidifies their position in the industry. By providing a compact realization of power management components, [Company Name] empowers system designers to meet the ever-increasing demands of space-constrained applications while maintaining high-level performance and efficiency.In conclusion, the introduction of [Company Name]'s high-density PCB layout for DC/DC converters marks a significant advancement in power management technology. With its ability to reduce power losses, enhance thermal management, and enable compact designs, this innovative solution opens up new possibilities for system designers across various industries. [Company Name] reaffirms its commitment to delivering cutting-edge solutions, empowering customers to thrive in a rapidly evolving technological landscape.###About [Company Name]:[Company Name] is a leading provider of advanced power management solutions for a wide range of industries. With a strong focus on innovation, reliability, and customer satisfaction, [Company Name] has established itself as a trusted partner for businesses worldwide. Their cutting-edge technologies and expert technical support ensure that customers receive optimal solutions tailored to their unique requirements. For more information on [Company Name]'s power management solutions, visit [website URL].
Exploring the Significance of TG150 Material in Circuit Board Design and Manufacturing
The Key Importance of TG150 Material in Printed Circuit Board ManufacturingIf you have ever been involved in circuit board design, you would understand the significance and crucial role played by the electronic substrate, commonly known as the epoxy substrate or rf4. This material not only provides the necessary structural framework for the circuit, but it also acts as a foundation for building circuits. Among the various materials available for printed circuit board (PCB) manufacturing, the TG150 material stands out as an exceptional choice due to its unique properties and benefits.Before delving into the details of TG150 material, it is important to understand the basic importance of the substrate material in the PCB manufacturing process. The substrate acts as the base for all the electronic components, ensuring stable support and electrical connections. It plays a pivotal role in determining the physical and electrical performance of the final circuit board.Now, let us focus on the TG150 material and why it is widely used in the industry.TG150 material, also known as FR-4 (Flame Retardant 4), is a type of glass-reinforced epoxy laminate that meets the standards set by the Institute of Printed Circuits (IPC). It has excellent thermal stability and provides reliable electrical insulation. The "TG" in TG150 stands for glass transition temperature, which refers to the point at which the resin in the epoxy substrate changes from a rigid to a soft state.One of the key advantages of TG150 material is its ability to withstand high temperatures. It has a glass transition temperature of 150°C, indicating that it can function reliably even in harsh operating conditions that involve elevated temperatures. This makes it an ideal choice for applications that demand thermal resilience, such as power electronics, automotive systems, and industrial control equipment.Moreover, TG150 material exhibits low dielectric loss and excellent electrical properties, making it suitable for high-speed communication circuits and devices. It ensures efficient signal transmission and reduces signal loss, allowing for enhanced performance and reliability of the circuit.Another significant benefit of TG150 material is its dimensional stability. It maintains its shape and size even when subjected to extreme temperature variations, ensuring that the PCB remains intact and functional. This stability also helps in maintaining consistent electrical characteristics, preventing any potential signal interference or distortion.Furthermore, TG150 material offers good mechanical strength and durability, making it resistant to deformation, bending, and impact. This robustness ensures that the circuit board can withstand various external forces and environmental conditions, further enhancing its reliability and longevity.In terms of PCB assembly, TG150 material provides excellent solderability, allowing for easy and reliable attachment of electronic components. It also offers good adhesion properties, enabling strong bonding between the substrate and the copper traces, ensuring efficient electrical conduction.The use of TG150 material in PCB manufacturing also contributes to environmental sustainability. It is a halogen-free material, meaning it does not contain harmful substances like chlorine or bromine, which are known to have adverse effects on human health and the environment. This attribute aligns with the global trend towards eco-friendly and green manufacturing practices.In summary, the TG150 material plays a critical role in the success of PCB manufacturing. Its high thermal stability, excellent electrical properties, dimensional stability, mechanical strength, and environmental friendliness make it a preferred choice for a wide range of applications. Whether it is for power electronics, automotive systems, or high-speed communication devices, TG150 material ensures reliable and efficient performance of the circuit board. With its versatile properties and consistent quality, TG150 material continues to be an indispensable component in the world of circuit board design and manufacturing.
Step-by-Step Guide to Creating a 4-Layer PCB
In today's digital age, technology has become an integral part of our daily lives. One of the most breakthroughs in technology is printed circuit board (PCB) designing. PCBs are the foundation of almost all electronic devices, from smartphones to laptops – you name it. A high-performance and reliable PCB should be well-designed and manufactured, or else it could lead to catastrophic consequences. To achieve a high-quality PCB, the 4-layer PCB is at the forefront.But what is a 4-layer PCB? Simply put, it has four layers of copper traces separated by an insulating layer, also known as a dielectric layer. Unlike its 2-layered counterpart, a 4-layer PCB offers a myriad of benefits. It enables a higher density of components, provides better and more stable signal integrity, allows for easier implementation of ground planes, and has a lower electromagnetic interference (EMI) and crosstalk. As a result, 4-layer PCBs are widely used in complex electronic systems, especially in high-speed communication applications.So, what is the process to make a 4-layer PCB? The first step is to start with the layout design. The designer uses PCB design software to create a schematic diagram, which is then translated into a physical design layout. Once this is done, the designer must choose a suitable substrate material – commonly FR-4 – and determine the thickness of the copper foil required.Next, the designer creates a drill template for each layer, which determines the location of the holes that will be drilled throughout the board. The board is then laminated together with adhesive, and the copper foil is etched away to create the layer's traces. An automated machine drills holes through the board at the specified locations, and the inner layers are aligned to the drill holes and laminated onto the previously assembled layers.Once the layers are assembled, the board is plated using electroplating, and a solder mask is added to provide insulation and protection to the copper traces. Lastly, the board is silk screened with the component placement legend, a code that displays each component's location and orientation.As the demand for technological devices continues to rise, the development of high-quality and reliable PCBs like the 4-layer PCB is crucial. In this regard, several manufacturers are investing in the development of advanced PCBs. One such company that has found considerable success in PCB design and manufacturing is [company name here].[Company name here] specializes in the design and production of high-quality PCBs that meet the demands of various industries. With years of experience in the industry, the company has been able to build an exceptional portfolio of solutions that cater to their clients' needs. They offer a wide range of PCB designs, including the 4-layer PCB.One of the company's unique features is their expertise in utilizing advanced software to design their PCBs, streamlining the entire manufacturing process, from design to production, and ensuring that their products adhere to the highest quality standards. Their deep knowledge on the various materials used for different types of PCBs has also placed them in a unique position to advise their customers on choosing the right materials for their projects.In conclusion, for most electronic devices, the PCB is the backbone, and as such, the demand for high-quality PCB design and manufacturing will continue to rise. The 4-layer PCB stands out as an excellent option for high-performance electronic systems, where reliability and stability are paramount. [Company name here] is an industry leader in PCB design and manufacturing, offering top-of-the-line solutions suited for varying industries.
Types of Printed Circuit Boards: Single-Sided, Double-Sided, Multilayer, and Flexible
Advanced Printed Circuit Boards and their Diverse ApplicationsPrinted Circuit Boards (PCBs) are a material foundation for constructing many electronic gadgets. The PCB manufacturing industry has been thriving for decades and continues to expand. Presently, PCBs are implemented in gadgets of almost every aspect of our daily lives. The intricate processes involved in manufacturing PCBs play a vital role in shaping the electronics manufacturing industry. Several varieties of PCBs are used as per the devices' usage, and each type of PCB has its unique set of characteristics and usage. Single-sided PCBs are the most elementary types available. The design of these PCBs has circuitry on only one side, with the other side blank, in contrast to double-sided PCBs that have circuitry on both sides. Most basic gadgets, such as toys, calculators, or radios, use single-sided PCBs, due to the ease of their manufacturing. Double-sided PCBs consist of circuitry on both sides of the board. Components can be mounted to both sides, making double-sided PCBs more adaptable than single-sided PCBs. Double-sided PCBs are widely used in applications such as printers, switchboards, and power supplies. They are more efficient, sizeable, and flexible compared to single-sided PCBs.Multilayer PCBs use multiple layers and more complex circuits. In terms of functionality, multilayer PCBs are a step ahead of single-sided PCBs and double-sided PCBs. They consist of a multi-layered substrate, which is made up of multiple layers of circuit boards, making it an ideal foundation for larger and more complicated technical equipment like computers and data servers. Multilayer PCBs can accommodate massive components and can provide more substantial power densities, allowing devices to conduct many functions.Flexible PCBs, as the name suggests, are flexible and can be molded into various shapes and sizes. They are usually constructed using flexible plastic materials that can withstand mechanical deformation. Flexible PCBs use conductive traces that include conductive ink, copper, or other metallic materials. The board's flexibility makes them versatile in various devices, including smartphones, printers, cameras, and medical equipment.(need remove brand name), a leading PCB manufacturer, is known for its state-of-the-art PCBs that meet the demands of continually evolving technology. The company has cutting-edge R&D laboratories that provide continual technical support to a broad range of industries, including aerospace, medical, automotive, and telecommunications. (need remove brand name)'s advanced PCBs are used in the electrical and the electronics industry globally. Their expertise and ability to deliver the best, high-quality work create long-term relationships with their clients.The application of PCBs is diverse and vast. Moreover, the number of applications and the uses of PCBs is continually increasing with the advancement of technology. Electronic manufacturing service providers, circuit board designers, and original equipment manufacturers can utilize PCBs in various industries. PCBs can be found in almost every electronic device, from smartphones, tablets, and laptops, to home appliances, surveillance systems, and automobiles.The PCB manufacturing industry must ensure the efficient and timely production of high-quality PCBs - an integral part of our daily lives. Companies must adhere to industry standards and regulations, comply with environmental legislation, and stay current with the development of new technologies to remain competitive.In conclusion, PCBs are crucial elements in the manufacturing of electronic devices. A wide range of PCBs available in the market caters to various gadget industries' needs. PCB manufacturers must take on the challenges of incorporating cutting-edge technology and manufacturing environmentally conscious PCBs while adhering to all industry standards and regulations. (need remove brand name) continues to lead the PCB manufacturing industry by providing advanced solutions to their clients' complex electronic challenges.
High-Quality PCBA for Home Automation Equipment Supplier in China
article:China PCBA Manufacturer Announces High-Quality PCBA for Home Automation EquipmentAs the world continues to move towards automation, home automation equipment has become increasingly popular for homeowners looking to optimize their homes. This trend can be seen all over the world, and the demand for high-quality home automation equipment has never been higher.In response to this demand, a China-based company specializing in PCBA (Printed Circuit Board Assembly) manufacturing is now offering innovative solutions for home automation equipment. The company offers a wide range of PCBA for different home automation applications, with a focus on providing high-quality and reliable components.The company's latest offering includes PCBA for home automation equipment such as smart thermostats, smart lighting systems, smart locks, remote control systems, and many more. The PCBA they produce is designed to meet the specific needs of their clients, combined with the latest technological advancements in the industry. This ensures that the resulting home automation equipment is reliable, efficient and easy to use.The PCBA for home automation equipment is made with high-quality materials and features cutting-edge technology. The components are designed to work together seamlessly, ensuring that the overall automation system works perfectly. What's more, the company's commitment to quality is unmatched in the industry, making them a reliable partner for any customer looking to build a safe and efficient smart home.In addition to their high-quality products, this leading China-based company also provides exceptional customer service. They are experienced in working with clients from all over the world, and they understand the importance of delivering high-quality PCBA to their customers. They work closely with customers to ensure that their unique requirements are met, and their expectations are exceeded.The company's state-of-the-art manufacturing facility is equipped with the latest technology, enabling them to produce high-quality products at an affordable price. They also have a dedicated team of professionals who are committed to delivering the best possible product to each customer.For customers looking to automate their homes, this China-based company provides the highest quality PCBA solutions available on the market today. Through their commitment to quality, innovation, and customer service, they have established themselves as a reliable partner to a growing number of customers in the home automation industry.In conclusion, with the continued growth of home automation, the demand for high-quality PCBA for home automation equipment is increasing. This demand, combined with a commitment to quality and innovation, has made this China-based PCBA manufacturer an industry leader in providing innovative solutions for smart homes. By offering a wide range of PCBA solutions, they are helping individuals and businesses to create safer and smarter homes for themselves and their families. Contact them today to learn more about their services and start building your smart home of tomorrow.
Latest News and Updates on PCB Contamination
- A Comprehensive Guide to Creating High-Quality PCBsPrinted Circuit Boards (PCBs) have become an essential component in the modern electronics industry. These boards serve as a foundation for electronic components, making them indispensable for manufacturing up-to-date devices that offer unprecedented functionality.As technology continues to advance, the demand for high-quality PCBs is only expected to increase. In this blog post, we'll explore some of the best practices for creating exceptional PCBs. We'll also touch on some of the important aspects to keep in mind when creating professional-grade PCBs.Factors to Consider When Creating PCBs1. The layout of the boardThe first step in creating a PCB is the layout. You'll want to ensure that the placement and routing of your components are optimal for their intended function. You should also consider the board size, shape, and thickness, as these factors can affect the performance and durability of the PCB.2. Material selectionThe materials used in creating the board are also crucial in determining the PCB's quality. Depending on your specific needs, you can choose from various materials, such as FR4, ceramic, and polyimide. The durability and temperature resistance of the board are factors that can be affected by your material selection.3. Traces and spacingClosely related to the board layout, the traces and spacing on the PCB play a significant role in its performance. The traces should be optimally sized and spaced for minimal interference and low resistance.4. DRC (Design Rule Check)A DRC, or Design Rule Check, is a software utility that validates a PCB design and checks it against industry-standard design rules. This essential step ensures that everything complies with specific guidelines and specifications, which can prevent costly errors in the final product.5. Documentation and specificationsCreating proper documentation and specifications is key to ensuring a smooth and efficient manufacturing process for your PCB. Proper documentation provides guidelines for other teams involved in PCB production. It also helps to ensure that the final product meets all necessary standards and requirements.Benefits of Creating High-Quality PCBs1. Enhanced performance and reliabilityHigh-quality PCBs are designed to meet specific requirements and standards, ensuring optimal performance and durability. They function to enhance signal integrity and reduce noise interference, resulting in improved reliability and stability.2. Cost-effectivenessWhile it might seem like investing more in the production of high-quality PCBs is costlier, the opposite can be true. High-quality PCBs are less likely to require repairs or replacements, reducing overall maintenance costs in the long run. Plus, because the PCBs are designed to meet specific requirements, there's less likelihood of production errors that can lead to critical system failure, which can be even more expensive.3. Improved product designCreating high-quality PCBs provides better signals and designs, which can lead to improved product design overall. High-quality PCBs can contribute to the overall functionality and aesthetic appeal of the end product.ConclusionCreating high-quality PCBs requires a keen understanding of specific aspects of PCB design. Taking the necessary steps to optimize your PCB design is critical to product success. From layout and material selection to trace spacing and DRC, ensuring that your PCB meets industry standards and requirements is non-negotiable. Finally, the proper documentation and specifications of your PCB help guide manufacturing, ultimately leading to a more cost-effective and efficient process.By keeping in mind the factors and benefits we've discussed in this blog post, you'll be well on your way to creating high-quality PCBs that meet industry standards and requirements.
Close-up of Components on a Printed Circuit Board (PCB) - High-Quality Stock Image
A printed circuit board (PCB), also known as a circuit board, is an essential component of any electronic device, whether it's a smartphone, a laptop, a television, or any other gadget. PCBs come in different shapes and sizes depending on the specific device’s design and function, but all serve the same purpose: to provide a platform for connecting various electronic components.A PCB is essentially a thin board made of insulating material (such as fiberglass or plastic) with a conductive layer printed on it. The conductive layer is usually made of copper, which is etched to create pathways (or traces) that connect different components. These components may include resistors, capacitors, diodes, transistors, and integrated circuits.Circuit boards are the backbone of modern electronics, and they’re becoming increasingly important as technology continues to evolve. They allow electronic devices to be smaller, lighter, and more efficient while providing more functionality. Without them, many of the devices we rely on today would not be possible.The design of a PCB is critical to its functionality and performance. The layout and spacing of components must be carefully planned to ensure that they don't interfere with each other and that the circuit operates correctly. Software tools are used to create PCB designs that allow engineers to simulate the circuit's behavior and optimize its performance.Once the PCB design is complete, the board is manufactured using specialized equipment that prints the conductive layer onto the insulating material and etches away the excess copper. The boards are then inspected for quality and tested to ensure that they function as designed.PCBs are used in a wide range of applications, from consumer electronics to industrial machinery. They’re also used in medical devices, aerospace components, and automotive systems. The automotive industry, in particular, relies heavily on PCBs for things like engine control units, airbag sensors, and entertainment systems.In conclusion, PCBs are a critical component of modern electronics and play a crucial role in the functionality and performance of electronic devices. They allow for smaller, more efficient devices with more advanced features. The design and manufacturing of PCBs require specialized skills, making them an important part of the electronics industry. As technology continues to evolve, PCBs will continue to play a crucial role in the development of new and innovative products.
In response to the need for improved protection of flexible circuits, a new method of double-sided soldermask application is becoming increasingly popular. Liquid photoimageable soldermask is now replacing older methods. To accommodate this change, technological advancements were necessary, leading to the development of the Smart Print System for coating and handling extremely thin flexible circuits.
: Meet the Demand for Double-Sided SoldermaskFlexible circuits have become increasingly popular in recent years due to their numerous benefits such as being lightweight, flexible, and easy to integrate into various products. They are widely used in industries such as aerospace, medical devices, consumer electronics and more. However, with more complex applications, the need for improved circuit protection has become paramount. This is where the double-sided soldermask comes in. What is Double-Sided Soldermask?Soldermask is a coating applied to the copper traces and pads on a printed circuit board (PCB). It is designed to protect the circuit during the assembly process and prevent unintended solder contacts. Traditionally, soldermask was applied to only one side of a PCB. However, with the growing demand for flexible circuits, the industry now requires double-sided soldermask, which is an insulating, protective coating applied to both sides of the flexible circuit.Why the Need for Double-Sided Soldermask?Double-sided soldermask is necessary for flexible circuits because these circuits are often bent, twisted, and shaped to fit into a variety of devices. As a result, the delicate circuits need protection not only on one side but on both sides to ensure their longevity. Without this added protection, the longevity and quality of the circuit may be compromised - and no one wants that. Advantages and Disadvantages of Double-Sided SoldermaskAdvantages:- Increased protection: Double-sided soldermask offers more comprehensive protection to flexible circuits, making them more durable and less prone to damage.- Enhanced performance: The protective coating can help to improve the electrical properties of the circuit and reduce the possibility of interference.- Flexibility: With the added protection, flexible circuits can be bent and manipulated with less risk of damage.Disadvantages: - More complex manufacturing: Double-sided soldermask adds an extra layer of complexity to the manufacturing process, driving up production costs and increasing the time required to complete the circuit.- More technical challenges: Applying the coating to both sides of the circuit can be tricky, especially when dealing with thin and flexible circuits.- Limited Availability: Not all manufacturers are equipped with the technology and knowledge to produce double-sided soldermask circuits.How Circuit Automation is Meeting the Demand?To meet the demand for double-sided soldermask, Circuit Automation developed and commercialized the DP3500 coater. This technology is specifically designed to handle and coat very thin flexible circuits, overcoming the technical challenges associated with this application. The liquid photoimageable soldermask technology used in the DP3500 coater enables the production of circuits with double-sided soldermask, providing better protection and long-lasting performance.The DP3500 coater is also equipped with the Smart Print System (SPS), which is a proprietary technology that ensures accurate and consistent coating thickness, even on delicate flexible circuits. The SPS allows for precision printing of the soldermask on both sides of the circuit, minimizing errors and improving the overall quality of the finished product. ConclusionIn summary, the demand for double-sided soldermask has been driven by the need for improved protection and durability of flexible circuits. While this technology adds complexity to the manufacturing process, it also offers significant benefits and helps to improve the overall performance of the circuit. Circuit Automation has answered the call by developing the DP3500 coater and the Smart Print System, making double-sided soldermask circuits accessible and affordable for a wide range of industries.
Essential Equipment Used in PCB Manufacturing
PCB Manufacturing Equipment List: What Is Used to Manufacture PCB?Printed circuit boards (PCBs) are essential components of modern electronic devices. Nearly every electronic gadget, appliance, or device has one or several PCBs at its core. These boards house electronic components that enable them to function efficiently.As PCBs continue to grow in demand and sophistication, so does the need for specialized equipment to manufacture them. PCB manufacturing is a complex process that requires the use of several types of equipment and machinery. Here's a PCB manufacturing equipment list that outlines the various machines and tools used in PCB production:1. PCB Design and Layout SoftwareThe first stage in PCB manufacturing is designing the board. Design engineers use specialized software to create the schematics and layout of the board. These programs help ensure the correct placement of components, trace routing, and board dimensions, among other things.2. CNC Drilling MachinesA CNC drill machine is used to create holes precisely at designated spots on the substrate. The machine drills the holes based on the design specifications in the PCB layout software.3. Etching and Stripping MachinesAfter drilling, the substrate is coated with a layer of copper. Next, an etching machine removes the unnecessary copper to create the copper traces and pattern on the board. The PCB is then transferred to a stripping machine, which removes the protective layer, leaving behind the copper traces and contact points.4. Solder Masking MachinesA layer of solder mask is applied to the PCB to protect the copper traces and contact points from oxidation and other environmental factors. The solder mask is also used to demarcate the proper placement and orientation of the electronic components.5. Silk Screen Printing MachinesPCBs often have markings that identify the manufacturer, product, or voltage of the device. Silk screen printing machines are used to print these markings and other essential information on the PCB.6. Pick-and-Place MachinesA pick-and-place machine is a robotic device that places electronic components onto the PCB. The machine picks up the components from a reel or tray and places them onto the board, based on the design specifications.7. Reflow OvensOnce all the components are placed onto the board, the PCB goes into a reflow oven. The oven heats the board to a temperature that melts the solder and binds the components to the board, creating a complete circuit.8. AOI and ICT Test EquipmentAfter the board is assembled, it undergoes testing to ensure that the components are correctly installed and that the circuit is functioning correctly. Two types of testing equipment are typically used: Automated Optical Inspection (AOI) and In-Circuit Testing (ICT) equipment.AOI equipment is used to visually inspect the board for defects, errors, and misaligned components. ICT equipment, on the other hand, tests the components on the board for functionality by sending electrical signals through the circuit.ConclusionOverall, PCB manufacturing is a complex process that requires the use of specialized equipment and machinery. From the design software to the final assembly, each step of the process relies on specific machines and tools to create a high-quality and reliable PCB.If you need PCB manufacturing for your electronic device, it's essential to work with a reputable and experienced PCB manufacturer that uses high-quality equipment and machinery. At (remove brand name), we utilize the latest techniques and equipment to produce the best PCBs for your needs. Contact us today to learn more about our PCB manufacturing services.