Bluetooth Integrated Circuit Board: Everything You Need to Know
By:admin
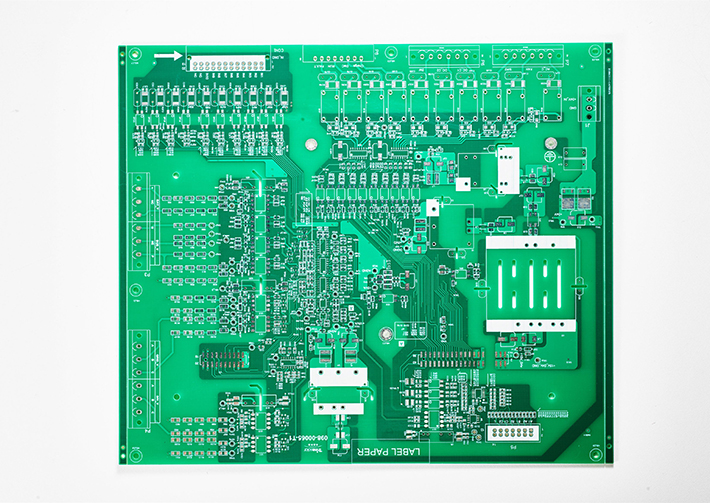
In the world of technology, there is a constant need for innovation and advancement. As we continue to rely more and more on wireless devices, the demand for improved connectivity and reliability also grows. This is where the Bluetooth PCB Board comes in, representing a significant breakthrough in wireless technology.
The Bluetooth PCB Board, developed by an industry-leading company, represents the latest advancement in Bluetooth connectivity. This cutting-edge technology is designed to provide seamless and reliable wireless communication, making it ideal for a wide range of applications, including consumer electronics, automotive, healthcare, and industrial automation.
This Bluetooth PCB Board boasts several key features that set it apart from other wireless connectivity solutions on the market. Firstly, it offers enhanced compatibility and interoperability, ensuring that it can seamlessly integrate with a wide range of devices and systems. This is essential for ensuring a smooth and efficient user experience, especially as the Internet of Things (IoT) continues to grow and connect more devices.
Moreover, this Bluetooth PCB Board also delivers superior performance in terms of range and data transfer speeds. This ensures that users can enjoy a fast and reliable wireless connection, whether they are streaming media, transferring files, or controlling IoT devices. This enhanced performance is made possible by the use of state-of-the-art components and advanced signal processing algorithms, which are integrated into the compact and efficient PCB design.
In addition to its technical capabilities, the Bluetooth PCB Board also offers a high level of flexibility and customization. This allows for seamless integration into a wide range of devices and systems, ensuring that it can meet the specific requirements of different applications. Whether it is used in a wearable fitness tracker, a smart home device, or a connected car, this Bluetooth PCB Board can be tailored to deliver optimal performance and functionality.
One of the key factors that sets this Bluetooth PCB Board apart is the company behind its development. With a strong track record of innovation and a commitment to excellence, the company has established itself as a leader in the field of wireless connectivity solutions. Drawing on years of experience and expertise, the company has been able to push the boundaries of what is possible with Bluetooth technology, delivering a solution that meets the evolving needs of the market.
Moreover, the company is dedicated to ensuring the highest standards of quality and reliability in all of its products. This commitment is reflected in the rigorous testing and validation processes that the Bluetooth PCB Board undergoes, ensuring that it meets and exceeds industry standards for performance and reliability. As a result, customers can have full confidence in the reliability and durability of this cutting-edge technology.
Looking ahead, the Bluetooth PCB Board is set to play a key role in shaping the future of wireless connectivity. As the demand for reliable, high-performance wireless solutions continues to grow, this technology is well-positioned to meet these needs and drive innovation in a wide range of industries. Whether it is enabling seamless audio streaming, supporting the growth of IoT devices, or enhancing connectivity in automotive and industrial applications, the Bluetooth PCB Board is poised to make a lasting impact.
In conclusion, the Bluetooth PCB Board represents a significant breakthrough in wireless technology, offering enhanced connectivity, reliability, and performance. Backed by an industry-leading company with a strong track record of innovation and excellence, this cutting-edge technology is set to drive the next wave of advancement in wireless connectivity. As the demand for reliable and high-performance wireless solutions continues to grow, the Bluetooth PCB Board is well-positioned to meet these needs and deliver a seamless and efficient user experience across a wide range of applications.
Company News & Blog
Rigid-Flex PCBs: The Ultimate Solution for Complex Circuit DesignsIn today's world, electronics are everywhere, from our phones to our cars and even our homes. The demand for compact and lightweight devices with high-speed performance increases day by day. To meet the requirements of current and future technologies, Printed Circuit Boards (PCBs) have evolved in different ways, and Rigid-Flex PCBs are one of the most significant advancements that have taken place. In this article, we will discuss Rigid-Flex PCBs, its working principle, and its benefits.What is a Rigid-Flex PCB?A Rigid-Flex PCB is a hybrid PCB that incorporates both rigid and flexible circuit materials. The circuit board is fabricated using a special manufacturing process that combines rigid PCB substrate and flexible PCB substrate into a single board. This combination provides a composite structure that can withstand harsh working conditions while reducing assembly time and cost. Rigid-Flex PCBs allow for reliable performance even in high-vibration and high-impact environments.Working Principle of Rigid-Flex PCBRigid-Flex PCB is an innovative design solution for a diverse range of applications. The working principle of Rigid-Flex PCB is based on combining rigid boards with flexible substrates. The rigid PCB provides a stable base for the device while the flexible PCBs act as connectors between components. Since the flexible PCBs can bend and fold without risking damage to the components, a single, compact and secure board can be formed.Benefits of Rigid-Flex PCBsRigid-Flex PCBs offer several benefits over traditional PCBs. Some of the key benefits are:1. Space Saving Design: Rigid-Flex PCBs save space compared to traditional PCB designs, making them ideal for applications where compact size is a requirement.2. Reduction in Assembly Time and Cost: Rigid-Flex PCBs allow for fewer interconnects and lower assembly costs due to their simple structure.3. Improved Reliability: Rigid-Flex PCBs have improved reliability in high-vibration and high-impact environments.4. Improved Thermal Management: Rigid-Flex PCBs offer better thermal conductivity through the entire board since it uses a combination of rigid and flexible materials.5. Improved Signal Integrity: Rigid-Flex PCBs offer better signal integrity since they have fewer connectors and fewer potential discontinuities in the signal path.Why Choose a Rigid-Flex PCB Manufacturer?When it comes to choosing a Rigid-Flex PCB manufacturer, it is essential to work with a manufacturer who has the expertise and technical know-how to incorporate the best Rigid-Flex PCB design practices. A reliable and experienced manufacturer will ensure that the board's design, layout, and materials meet the specific requirements of the application.ConclusionRigid-Flex PCBs are an innovative and practical solution for many applications due to their excellent reliability, improved thermal management, and space-saving design. Choosing the right Rigid-Flex PCB manufacturer ensures that the design meets the specific requirements of your application. When it comes to choosing a manufacturer that specializes in Rigid-Flex PCBs, it is best to choose Hitech Circuits Co., Ltd. for your circuit board needs.
Copper Clad Printed Circuit Boards: A Guide to Their Manufacturing and Applications
The demand for advanced electronics continues to rise, driving the need for high-performance printed circuit boards (PCBs). As a leading manufacturer in the industry, {Company Name} is proud to introduce its latest innovation: the Copper Clad Printed Circuit Board.{Company Name} has been at the forefront of PCB production for over a decade, consistently delivering cutting-edge solutions to meet the evolving needs of the electronics market. With a commitment to quality, innovation, and customer satisfaction, the company has garnered a reputation for excellence in the industry.The new Copper Clad Printed Circuit Board represents a significant advancement in PCB technology. By incorporating a high-quality copper layer, the PCB offers enhanced conductivity, reliability, and durability. This innovative design allows for faster signal transmission and greater overall performance, making it ideal for a wide range of applications, from consumer electronics to industrial machinery."We are thrilled to introduce our Copper Clad Printed Circuit Board to the market," said {Spokesperson}, the CEO of {Company Name}. "This product is the result of extensive research and development, and we believe it will set a new standard for PCB performance and reliability. We are confident that it will exceed the expectations of our customers and provide them with a competitive edge in their respective industries."In addition to its superior technical specifications, the Copper Clad Printed Circuit Board is also designed with ease of manufacturing in mind. {Company Name} has optimized the production process to ensure efficient and cost-effective manufacturing, allowing for seamless integration into a variety of electronic devices and systems.With a growing demand for high-performance electronics, the introduction of the Copper Clad Printed Circuit Board comes at an opportune time. As industries continue to push the boundaries of technological innovation, the need for reliable and efficient PCBs has never been greater. {Company Name} is poised to meet this demand with its latest offering, further solidifying its position as a leader in the industry.The launch of the Copper Clad Printed Circuit Board is a testament to {Company Name}'s ongoing commitment to excellence and innovation. The company's dedication to research and development has allowed it to stay ahead of the curve, consistently delivering groundbreaking solutions to its customers. Through its investments in cutting-edge technology and manufacturing processes, {Company Name} has positioned itself as a trusted partner for businesses seeking top-of-the-line PCB solutions.Looking ahead, {Company Name} is eager to see the impact of its Copper Clad Printed Circuit Board on the electronics market. With its unparalleled performance and reliability, the PCB is anticipated to become a go-to choice for manufacturers across various industries. As the company continues to push the boundaries of what is possible in PCB technology, it remains committed to delivering exceptional products and service to its customers.In conclusion, the introduction of {Company Name}'s Copper Clad Printed Circuit Board marks a significant milestone in the company's ongoing pursuit of innovation and excellence. With its unmatched performance, reliability, and manufacturing efficiency, the PCB is poised to make a lasting impact on the electronics industry. As demand for advanced electronics continues to grow, {Company Name} is well-positioned to meet the needs of customers seeking high-quality PCB solutions.
Unveiling the Latest Breakthrough: Harnessing the Power of FR4 Tg150 Technology
Innovative PCB Material Sets New Standards for Electronics IndustryWith a mission to constantly push the boundaries of technological advancements, a leading company in the electronics industry has recently introduced a groundbreaking PCB material known as FR4 TG150. Demonstrating a commitment to quality and innovation, this remarkable product is set to revolutionize the way electronic devices are designed and manufactured.The FR4 TG150, a cutting-edge PCB material, addresses the escalating demands of modern electronics. This high-performance material offers superior reliability, increased efficiency, and enhanced durability, making it highly sought after by engineers and manufacturers alike. The material's unique properties make it particularly well-suited for use in various applications, ranging from consumer electronics to industrial machinery.One of the key features that sets FR4 TG150 apart from traditional PCB materials is its exceptional thermal stability. By ensuring excellent heat resistance, this innovative material enables electronic devices to function optimally in the most demanding environments. With the rapid growth of technology, devices often face challenging conditions such as high temperatures or fluctuating thermal cycles. FR4 TG150 mitigates these concerns, making it an ideal choice for mission-critical applications.Furthermore, the FR4 TG150 also offers excellent mechanical strength and insulation properties. This enables it to withstand physical stress, reducing the risk of damage or failure during operation. By providing a high degree of reliability, the material proves itself as a formidable solution for industries where robustness and long-term functionality are paramount.In terms of electrical performance, FR4 TG150 excels in delivering superior signal integrity. Its low electrical loss allows for faster signal propagation and reduced signal distortions. This is particularly advantageous for high-speed digital circuits found in modern electronic devices. By minimizing signal degradation, the material ensures a higher level of accuracy and functionality, ultimately enhancing the overall user experience.The inherent versatility of FR4 TG150 makes it an ideal choice for various electronic applications. From smartphones and tablets to automotive electronics and aerospace systems, the material's adaptability meets the diverse needs of different industries. This enables engineers and designers to explore new possibilities, enabling the development of innovative and cutting-edge products.The introduction of FR4 TG150 heralds a new era in the electronics industry, propelling it towards greater heights. Industry experts are touting this revolutionary material as a game-changer, setting new standards for PCB manufacturing and design. With its exceptional thermal stability, mechanical strength, insulation properties, and electrical performance, FR4 TG150 is poised to redefine the benchmark for future electronic devices.As a leading company dedicated to providing comprehensive solutions for the electronics industry, the manufacturer of FR4 TG150 reaffirms its commitment to innovation and quality. Through relentless research and development efforts, they aim to empower engineers and manufacturers with groundbreaking solutions that meet the evolving demands of the digital age.In conclusion, FR4 TG150 represents an extraordinary advancement in PCB materials. Its exceptional properties and versatility make it a game-changer in the electronics industry. As this innovative material gains traction, it is expected to transform the way electronic devices are designed, manufactured, and experienced. With a company at the forefront of this technological revolution, the future of electronics looks promising, ushering in a new era of excellence.
Professional Manufacturer and Supplier of Thick Copper PCB Boards in China
and Heavy Copper Pcb Suppliers.Heavy Copper PCB: Essential in High Power, High Temperature ApplicationsHeavy Copper PCB or Thick Copper PCB is a printed circuit board (PCB) with copper conductive layers above 4 Oz (140 µm). The thickness of copper in Heavy Copper PCB ranges from 4 Oz up to 20 Oz (700 µm), which is almost 12 times thicker than the usual copper thickness in standard PCBs. Heavy Copper PCBs are essential in applications that require high power, high temperature, and high mechanical stability.Applications of Heavy Copper PCBHeavy Copper PCB is widely used in a variety of applications that require higher than typical current carrying capabilities, better thermal performance, and increased durability. Some of the essential applications of Heavy Copper PCB include:1. Power Electronics:Heavy Copper PCBs play a vital role in high power electronics such as motor drives, inverters, and power converters. They provide the required thermal dissipation, thereby enhancing the efficiency, reliability, and stability of power electronics.2. Automotive Industry:Heavy Copper PCBs find extensive applications in the automotive industry where they are used in systems such as ABS, EPS, TPMS, and Engine Control Units (ECUs). They have excellent heat dissipation abilities and can withstand high mechanical stresses, ensuring that the electronic systems in vehicles operate efficiently and reliably.3. Aerospace:Heavy Copper PCBs are also used in the aerospace industry in applications such as satellites, radar systems, and communication systems. Their high thermal performance, high current carrying capacity, and high durability make them ideal for use in harsh environments.4. LED Lighting:Heavy Copper PCB is an essential component in LED lighting systems. They facilitate better thermal management, provide higher current carrying capacity, and make it possible to manufacture smaller and more efficient lighting systems.Why Choose Hitech Circuits as Your Heavy Copper PCB Supplier?Hitech Circuits is a professional Heavy Copper PCB manufacturer and supplier based in China. Our company has been involved in the production of Heavy Copper PCBs since 2000, and we have established ourselves as a leading supplier in this industry. Here are some reasons why you should choose Hitech Circuits as your Heavy Copper PCB supplier:1. High-quality products:Our Heavy Copper PCBs are manufactured using high-quality materials and advanced manufacturing techniques. We strictly adhere to industry standards and regulations, ensuring that our products meet the highest quality standards.2. Wide Range of Products:We offer a wide range of Heavy Copper PCB products, including multilayer Heavy Copper PCB, single-layer Heavy Copper PCB, and double-layer Heavy Copper PCB. We also provide customized solutions tailored explicitly to your requirements.3. Competitive Pricing:We offer competitive pricing without compromising on quality. Our pricing is structured to provide the best value for money in the industry.4. Experienced and Dedicated Team:Our team of experts has years of experience in Heavy Copper PCB manufacturing and design. We are committed to providing our customers with the best solutions and support throughout the entire production process.5. Excellent Customer Service:We pride ourselves on providing excellent customer service and support. Our dedicated customer service team is always available to assist you with any queries or concerns you may have.In conclusion, Heavy Copper PCBs are essential in high power, high temperature, and high mechanical stability applications. Hitech Circuits is a professional Heavy Copper PCB manufacturer and supplier offering high-quality products, a wide range of products, competitive pricing, experienced and dedicated team, and excellent customer service. Contact us today to learn more about how we can meet your Heavy Copper PCB needs.
Types of Printed Circuit Boards: Single-Sided, Double-Sided, Multilayer, and Flexible
Advanced Printed Circuit Boards and their Diverse ApplicationsPrinted Circuit Boards (PCBs) are a material foundation for constructing many electronic gadgets. The PCB manufacturing industry has been thriving for decades and continues to expand. Presently, PCBs are implemented in gadgets of almost every aspect of our daily lives. The intricate processes involved in manufacturing PCBs play a vital role in shaping the electronics manufacturing industry. Several varieties of PCBs are used as per the devices' usage, and each type of PCB has its unique set of characteristics and usage. Single-sided PCBs are the most elementary types available. The design of these PCBs has circuitry on only one side, with the other side blank, in contrast to double-sided PCBs that have circuitry on both sides. Most basic gadgets, such as toys, calculators, or radios, use single-sided PCBs, due to the ease of their manufacturing. Double-sided PCBs consist of circuitry on both sides of the board. Components can be mounted to both sides, making double-sided PCBs more adaptable than single-sided PCBs. Double-sided PCBs are widely used in applications such as printers, switchboards, and power supplies. They are more efficient, sizeable, and flexible compared to single-sided PCBs.Multilayer PCBs use multiple layers and more complex circuits. In terms of functionality, multilayer PCBs are a step ahead of single-sided PCBs and double-sided PCBs. They consist of a multi-layered substrate, which is made up of multiple layers of circuit boards, making it an ideal foundation for larger and more complicated technical equipment like computers and data servers. Multilayer PCBs can accommodate massive components and can provide more substantial power densities, allowing devices to conduct many functions.Flexible PCBs, as the name suggests, are flexible and can be molded into various shapes and sizes. They are usually constructed using flexible plastic materials that can withstand mechanical deformation. Flexible PCBs use conductive traces that include conductive ink, copper, or other metallic materials. The board's flexibility makes them versatile in various devices, including smartphones, printers, cameras, and medical equipment.(need remove brand name), a leading PCB manufacturer, is known for its state-of-the-art PCBs that meet the demands of continually evolving technology. The company has cutting-edge R&D laboratories that provide continual technical support to a broad range of industries, including aerospace, medical, automotive, and telecommunications. (need remove brand name)'s advanced PCBs are used in the electrical and the electronics industry globally. Their expertise and ability to deliver the best, high-quality work create long-term relationships with their clients.The application of PCBs is diverse and vast. Moreover, the number of applications and the uses of PCBs is continually increasing with the advancement of technology. Electronic manufacturing service providers, circuit board designers, and original equipment manufacturers can utilize PCBs in various industries. PCBs can be found in almost every electronic device, from smartphones, tablets, and laptops, to home appliances, surveillance systems, and automobiles.The PCB manufacturing industry must ensure the efficient and timely production of high-quality PCBs - an integral part of our daily lives. Companies must adhere to industry standards and regulations, comply with environmental legislation, and stay current with the development of new technologies to remain competitive.In conclusion, PCBs are crucial elements in the manufacturing of electronic devices. A wide range of PCBs available in the market caters to various gadget industries' needs. PCB manufacturers must take on the challenges of incorporating cutting-edge technology and manufacturing environmentally conscious PCBs while adhering to all industry standards and regulations. (need remove brand name) continues to lead the PCB manufacturing industry by providing advanced solutions to their clients' complex electronic challenges.
This New PCB-making Technique Lets You Turn Almost Any Plastic Surface into a Circuit Board
article about a new process for creating PCBs using a plating solution.The process, developed by a company called CircuitMaker, involves applying a conductive plating solution to a plastic surface, and selectively etching away the plating to create the desired circuit pattern. The solution is said to work on a range of plastics, including ABS, polycarbonate, and acrylic.According to CircuitMaker, the process offers several advantages over traditional PCB fabrication methods. First, it allows for more flexibility in the design process, as the plating can be applied to irregular or non-flat surfaces. Second, it can be done using relatively simple equipment, such as a hobbyist-grade laser cutter and an electroplating kit. And third, it can be done quickly and cheaply, with a total cost of under $10 per board.The video posted by Krasnow demonstrates the process in action, showing him creating a simple LED circuit on a plastic toy using the plating solution. He begins by creating a design in Eagle CAD, then exporting it to a laser cutter to create a template. Next, he applies the conductive plating solution to the plastic surface, using a brush to ensure even coverage. He then places the template over the plating and exposes it to light, causing the solution to harden.Once the plating has hardened, Krasnow removes the template and wipes away any excess solution. He then places the plastic in an electroplating bath, which selectively dissolves the plating to create the circuit pattern. Finally, he cleans the board and solders the components in place.While the CircuitMaker process may not replace traditional PCB fabrication techniques for complex or high-density circuits, it could certainly be useful for hobbyists or small-scale manufacturers looking for a simple and inexpensive way to create basic circuits. It also has the potential to open up new applications for PCBs, such as embedding them in non-traditional materials like clothing or toys.Of course, there are also some drawbacks to the process. The plating solution can be messy and difficult to work with, and it may not be as reliable or durable as a traditional board. Additionally, it may be difficult to achieve precise trace widths or spacing using this method.Overall, the CircuitMaker process seems like an interesting and potentially useful addition to the PCB fabrication toolkit. It will be interesting to see how it develops and whether it finds a place in the wider electronics community.
Boosting Efficiency and Reliability: A Comprehensive Guide to Through Hole Assembly
Through Hole Assembly Revolutionizes Electronics ManufacturingThe field of electronics has witnessed a tremendous evolution over the years, with new technologies constantly reshaping the industry. Among these innovations, Through Hole Assembly has emerged as a game-changer in the realm of electronics manufacturing. Its numerous benefits and advancements have significantly improved the production process, making it more efficient and reliable.Through Hole Assembly, also known as THA, is a method of mounting electronic components onto a printed circuit board (PCB). Unlike its predecessor, Surface Mount Technology (SMT), THA involves components being inserted through holes drilled into the PCB, and then soldered onto the opposite side. This process ensures stronger mechanical connections, allowing the PCB to withstand more rigorous conditions, including high temperatures and vibrations.One key advantage of Through Hole Assembly is the secure and robust connection it provides. By relying on the PCB's plated through holes, components are less likely to detach during use, making THA ideal for applications where durability is paramount. Industries such as automotive, aerospace, and military heavily rely on Through Hole Assembly to ensure their electronics can withstand extreme conditions while maintaining optimal functionality.Furthermore, Through Hole Assembly accommodates larger components that cannot be used in Surface Mount Technology. These components often require higher power handling capabilities, making THA the go-to method for devices requiring enhanced performance. Moreover, THA grants manufacturers the flexibility to work with a wide range of component sizes or even mix different types within the same PCB, further expanding design possibilities.Additionally, Through Hole Assembly simplifies repair and modification procedures. In some occasions, components might fail or need replacement during the lifetime of a product. With SMT technology, the de-soldering and re-soldering process can be complex and risky, potentially damaging nearby surface-mounted components. THA simplifies this process by allowing easy removal and replacement of individual components, minimizing the risk of unintentional collateral damage.While Through Hole Assembly's advantages are plentiful, it has faced challenges due to the emergence of Surface Mount Technology, which quickly gained popularity in the electronics industry. The smaller size of SMT components allows for higher packing density on PCBs, reducing production costs and enabling miniaturization of devices. Consequently, many manufacturers favored SMT over THA, leading to a decline in Through Hole Assembly's usage.However, recent advancements in Through Hole Assembly technology have rekindled interest in this assembly method. Industry leader {} has introduced innovative solutions that address the limitations associated with THA, providing manufacturers with the flexibility and cost-effectiveness that rival Surface Mount Technology.With its dedication to pushing boundaries, {} has developed through-hole components that are smaller, slimmer, and more versatile, significantly increasing the packing density on a PCB. This breakthrough allows manufacturers to achieve the best of both worlds - strong mechanical connections and high component density. As a result, Through Hole Assembly has once again become an attractive option for various industries, enabling them to meet the demands of their customers while maintaining robust designs.Moreover, {} has implemented automation technologies to streamline the Through Hole Assembly process. Automated component insertion machines, robotic soldering, and efficient inspection systems have vastly improved productivity, reducing the time required for assembly. This increased efficiency not only saves on manufacturing costs but also allows for faster turnaround times, meeting the ever-growing demand for electronic devices.In conclusion, Through Hole Assembly has made a significant impact on electronics manufacturing. Its superior mechanical connections, compatibility with larger components, and ease of repair make it a preferred choice for industries where reliability and durability are paramount. With the recent advancements introduced by {}, Through Hole Assembly has become more versatile and cost-effective, proving that it continues to revolutionize the way electronic devices are manufactured.
Top Quality Printed Circuit Boards for HDI Technology Unveiled in Latest News Update
[Your Name][News Organization][Date][Headline][Subheading][City/Location] - [Company Name], a leading manufacturer of HDI Printed Circuit Boards (PCBs), has announced the launch of its latest range of high-density interconnect solutions. With a focus on innovation and advanced technology, [Company Name] aims to redefine the PCB industry by delivering cutting-edge products that offer improved performance and functionality.Established over [number] years ago, [Company Name] has evolved into a key player in the electronics manufacturing sector. The company's commitment to research and development has led to the creation of state-of-the-art HDI PCBs that drive the advancement and integration of various technologies.HDI PCBs play a crucial role in enabling smaller, lighter, and more complex electronic devices. They offer multiple benefits, including increased routing density, improved signal integrity, signal reliability, and enhanced thermal performance. With advancements in technology, the demand for HDI PCBs has surged, particularly in industries such as telecommunications, automotive, aerospace, and consumer electronics.[Company Name] recognizes this growing demand and has invested heavily in research and development to remain at the forefront of the industry. The company's team of experts continuously explores new materials, manufacturing techniques, and design methodologies to deliver innovative solutions that exceed customer expectations.One of the key features of [Company Name]'s HDI PCBs is their high routing density. By utilizing microvias and advanced layer stacking techniques, the company can achieve significant reduction in PCB footprint while maintaining signal integrity and performance. This allows electronic manufacturers to design and produce smaller and more compact devices without compromising functionality.Additionally, [Company Name] places great emphasis on the quality and reliability of its HDI PCBs. The company adheres to strict quality control measures at every stage of the manufacturing process, ensuring that each PCB meets the highest industry standards. By using cutting-edge manufacturing equipment and employing skilled technicians, [Company Name] guarantees consistent and reliable performance in its products.Furthermore, [Company Name]'s commitment to sustainability sets it apart from its competitors. The company strives to minimize its environmental impact by adopting eco-friendly practices throughout the manufacturing process. This includes using lead-free materials, implementing energy-efficient technologies, and recycling waste materials. By prioritizing sustainability, [Company Name] not only contributes to preserving the environment but also aligns itself with the growing global trend of responsible manufacturing.At present, [Company Name] serves a global client base, providing HDI PCBs to customers in various sectors across [number of countries]. The company's dedication to customer satisfaction, combined with its ability to offer tailored solutions, has earned it a solid reputation within the industry. Whether it's designing prototypes or mass-producing PCBs, [Company Name] works closely with its clients to understand their specific requirements and deliver customized solutions.With the launch of its latest range of HDI PCBs, [Company Name] is set to revolutionize the electronics industry. The company's commitment to innovation, quality, and sustainability ensures that its products meet and exceed the evolving needs of customers worldwide. As technology continues to evolve at a rapid pace, [Company Name] remains dedicated to pushing boundaries and powering the future of electronic devices.Contact:[Company Name]Address:Phone:Email:Website:Note: This news article is a sample and should be customized as per the specific requirements and guidelines of your news organization.
Leading manufacturers of Heavy Copper PCBs for high-power applications
Heavy Copper PCB Manufacturers Continues to Lead the Industry with Innovation and QualityIn today's fast-paced and ever-changing electronic industry, the demand for high-quality and durable printed circuit boards (PCBs) continues to grow. As a leading manufacturer in this field, Heavy Copper PCB Manufacturers has been at the forefront of producing top-of-the-line PCBs that meet the demanding requirements of various industries. With their commitment to innovation, quality, and customer satisfaction, Heavy Copper PCB Manufacturers has solidified its position as a trusted and reliable provider of heavy copper PCBs.Established in {year}, Heavy Copper PCB Manufacturers has continuously strived to push the boundaries of what is possible in PCB manufacturing. Through their state-of-the-art facilities and cutting-edge technology, they have been able to produce heavy copper PCBs that are not only strong and durable but also incredibly efficient. This has made them the go-to choice for many industries such as aerospace, automotive, telecommunications, and more.One of the key factors that set Heavy Copper PCB Manufacturers apart from its competitors is its unwavering commitment to quality. They adhere to strict quality control measures throughout the entire manufacturing process, ensuring that each heavy copper PCB that leaves their facility meets the highest standards. This dedication to quality has earned them a stellar reputation in the industry and has resulted in a loyal customer base that continues to rely on their products for their most critical applications.Furthermore, Heavy Copper PCB Manufacturers has been at the forefront of innovation in the PCB industry. They invest heavily in research and development to stay ahead of the curve and to anticipate the evolving needs of their customers. This has allowed them to develop cutting-edge manufacturing techniques and processes that have revolutionized the way heavy copper PCBs are produced. By staying innovative, they have been able to offer their customers solutions that not only meet their current requirements but also future-proof their designs.In addition to their commitment to quality and innovation, Heavy Copper PCB Manufacturers has also made customer satisfaction a top priority. They understand the importance of building strong partnerships with their customers and strive to provide them with exceptional service and support. Their team of knowledgeable and experienced professionals works closely with customers to understand their specific needs and requirements, offering tailored solutions that exceed expectations. This has earned them the trust and loyalty of their customers, who continue to turn to Heavy Copper PCB Manufacturers for all their heavy copper PCB needs.Looking ahead, Heavy Copper PCB Manufacturers is poised to continue leading the industry with its unwavering dedication to quality, innovation, and customer satisfaction. With a strong focus on research and development, they are committed to staying at the forefront of technological advancements and to anticipating the changing needs of the industry. By doing so, they are well-positioned to continue providing their customers with the most advanced and reliable heavy copper PCB solutions.In conclusion, Heavy Copper PCB Manufacturers has established itself as a leader in the PCB industry by consistently delivering high-quality, innovative, and reliable heavy copper PCBs. With a steadfast commitment to quality, a focus on innovation, and a dedication to customer satisfaction, they have earned the trust and loyalty of their customers. As they continue to push the boundaries of what is possible in PCB manufacturing, Heavy Copper PCB Manufacturers is set to remain the go-to choice for heavy copper PCBs for years to come.
and Pcb Prototype Assembly services.If you're in the market for PCB components and prototype assembly services, you've come to the right place. At (removed brand name), we understand the complexity and challenges of developing high-quality printed circuit boards.As a leading provider of PCB components and prototype assembly services, we have the expertise and resources to bring your project to life. From component procurement to mixed technology and SMT assembly, we specialize in delivering turnkey solutions that meet the unique needs of each of our clients.Here's what you can expect when you partner with us:Component ProcurementOur team of experts understands that sourcing high-quality components is essential to the success of any PCB project. We have a vast network of suppliers and are experienced in working with a wide range of components, including resistors, capacitors, diodes, transistors, and more.We only work with trusted suppliers to ensure that each component we use in our prototypes and assemblies is of the highest quality. We can procure components for both low- and high-volume projects and ensure that each one meets the necessary specifications.Through-Hole AssemblyWhile SMT assembly is an increasingly popular option, many projects still require through-hole assembly. This method involves inserting components into drilled holes on the board and then soldering them in place.Our team has years of experience in through-hole assembly and can handle projects of any size and complexity. We use state-of-the-art equipment and follow best practices to ensure that each component is placed and soldered accurately.Mixed Technology AssemblyMixed technology assembly is a hybrid of through-hole and SMT assembly. It allows for a combination of components to be used, including through-hole and SMT components, which can help reduce manufacturing costs while still meeting the necessary requirements.At (removed brand name), we specialize in mixed technology assembly and can work with a wide range of components to meet your specific needs. Our experts understand the unique challenges of mixed technology assembly and can help you design a custom PCB that works for your project.SMT AssemblySurface mount technology (SMT) assembly is increasingly popular and involves mounting components directly onto the surface of the board. It is an efficient and cost-effective method of assembly that allows for smaller, more compact designs.Our team of experts has extensive experience in SMT assembly and can handle projects of any size. We use state-of-the-art equipment and follow best practices to ensure that each component is placed accurately and securely.In conclusion, at (removed brand name), we understand the importance of high-quality PCB components and prototype assembly services to the success of your project. With expert component sourcing, through-hole and SMT assembly, mixed technology assembly, and turnkey solutions, we have the expertise and resources to bring your project to life. Contact us today to learn how we can help you realize your project's full potential.