- Home
- Blog
- Top Supplier of High-Quality Rigid-Flex PCBs in China - Affordable Prices, Reliable Products
Top Supplier of High-Quality Rigid-Flex PCBs in China - Affordable Prices, Reliable Products
By:admin
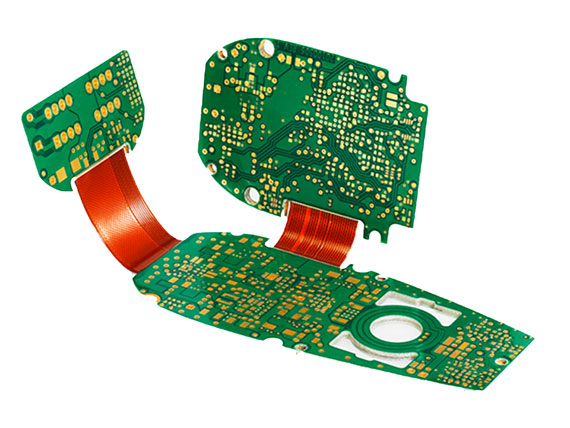
, Flex Pcb Board, Rigid-Flex Pcb, Rounded Rigid-Flex Pcb, Green Rigid-Flex Pcb, Complex Rigid-Flex Pcb.
As technology continues to evolve, the demand for more advanced and innovative printed circuit boards (PCBs) continues to arise. Rigid-Flex PCB is one of the most popular and highly demanded PCBs in the market today. The unique design of Rigid-Flex PCB offers an advantage over traditional PCBs because it can bend and flex without sacrificing its structural integrity.
A Rigid-Flex PCB is a combination of a rigid PCB board and a flexible PCB board. The combination of these two types of PCBs is what makes this type of board unique. The rigid portion of the board is designed to hold the components that require a stable surface. It is used to hold the electronic components and provide the structural support needed to keep them in place. On the other hand, the flexible portion of the board is designed to bend and flex without breaking.
Some of the most popular types of Rigid-Flex PCBs include Rounded Rigid-Flex PCB, Green Rigid-Flex PCB, and Complex Rigid-Flex PCB.
Rounded Rigid-Flex PCB is a type of Rigid-Flex PCB that has rounded corners. This type of PCB has a more aesthetic appeal and can be used in applications that require a more visually appealing board design. Its design offers an advantage because it can fit into tight spaces and reduces the chances of wear and tear on the board due to rough edges.
Green Rigid-Flex PCB is a type of board that has a green color. This color is obtained by using a green solder mask. Green is one of the most popular colors for printed circuit boards because it is easy to distinguish and identify. Green Rigid-Flex PCB is commonly used in applications such as communication and networking equipment.
Complex Rigid-Flex PCB is a type of Rigid-Flex PCB that has a more complicated design. It is used for applications that require more advanced circuitry and components. It is also used for applications that require multiple layers of circuits to be interconnected.
In conclusion, Rigid-Flex PCB offers numerous advantages over traditional PCBs. Its ability to bend and flex without breaking makes it ideal for applications that require durability and flexibility. Whether you are looking for Rounded Rigid-Flex PCB, Green Rigid-Flex PCB, or Complex Rigid-Flex PCB, a reliable supplier such as (brand name removed) can provide you with high-quality Rigid-Flex PCBs that meet your needs.
Company News & Blog
High-Quality Aluminium Board PCB Manufacturer, Supplier, and Factory in China - Circuit Boards for Sale
China-based Manufacturer Offers High-Quality Aluminium Board PCBs for Global MarketWith over 30 years of experience in the industry, a prominent China-based manufacturer and supplier is proud to offer top-notch Aluminium Board PCBs designed for optimal performance. Boasting refined processes and a commitment to quality, the company stands out as a leading provider of state-of-the-art PCB products for clients worldwide.The Aluminium Board PCBs are precision-engineered to deliver superior performance, durability, and reliability. Made from the finest aluminium materials, these PCBs are perfect for a wide range of applications, including high-speed data transmission, power management, and digital circuitry. Additionally, they are designed with exceptional thermal management capabilities, making them ideal for use in environments that require high temperatures and extreme conditions.The unique manufacturing process used by the company ensures that the Aluminium Board PCBs meet the highest industry standards and are of the highest quality. Whether clients are looking for standard PCBs or need a custom solution, the company has the expertise and experience to meet their needs. Furthermore, the PCBs are RoHS compliant, ensuring that they adhere to environmental and safety standards.One of the key features of the Aluminium Board PCBs is their remarkable resistance to environmental conditions, making them an ideal choice for a wide range of industrial applications. With exceptional thermal conductivity and excellent heat dissipation properties, these PCBs are able to maintain optimal performance at all times.The company's commitment to quality and innovation has made them a preferred choice for businesses around the world. Their attention to quality throughout the PCB production process, from design to assembly, ensures that only high-quality products are delivered to clients. This dedication to quality sets them apart from other PCB assembly companies and provides peace of mind to clients, employees, and R&D professionals relying on their products for prototyping and production.In addition to the unparalleled quality of their Aluminium Board PCBs, the company is also dedicated to providing fast turnaround times for orders. This means that clients can expect their PCBs to be delivered as agreed upon and as early as possible, allowing them to meet their project deadlines without delays.Clients who have used the Aluminium Board PCBs have praised their high quality and reliability. The PCBs feature a strong aluminium base that offers exceptional heat dissipation, ensuring that electronic devices stay safe and cool. Additionally, the boards are lightweight and easy to work with, making them a popular choice for DIY electronics enthusiasts.According to Ms. Angela Her, a satisfied customer, "The Aluminium Board PCB is a must-have for any electronics enthusiast. This innovative product is designed to offer optimal performance and durability, making it perfect for use in various electronic devices. Its high-quality materials ensure that it can withstand even the toughest of conditions."The company's commitment to providing high-quality Aluminium Board PCBs has positioned them as a preferred supplier for businesses and projects requiring reliable and efficient circuit boards. Their customizable solutions and dedication to customer satisfaction make them a trusted partner for clients around the world.In conclusion, the China-based manufacturer and supplier is proud to offer high-quality Aluminium Board PCBs designed for a wide range of applications. With a commitment to quality, innovation, and customer satisfaction, the company has solidified its position as a leading provider of state-of-the-art PCB products. Businesses and projects in need of reliable and efficient circuit boards can confidently turn to this manufacturer for their PCB needs.
Manufacturer and Supplier of Buried and Blind Vias - Factory Direct
As a seasoned manufacturer of Printed Circuit Boards, with over 30 years of experience, Omni PCB is known for offering state-of-the-art PCBs to meet the needs of various industries. The company has refined its processes to ensure the highest quality PCB products are delivered in the shortest possible time. Quality and efficiency are the core principles that guide their operations, ensuring that clients receive top-quality PCBs as agreed upon and as early as possible, meeting the demands of R&D work and prototyping.One of the key products that Omni PCB specializes in is Buried and Blind Vias, a crucial component in the modern electronic industry. These innovative solutions allow for the creation of complex and sophisticated circuitry designs without sacrificing board space. By using buried and blind vias, engineers can fully optimize their designs and reduce the number of layers needed in a PCB, making it an essential technology for modern-day electronics.Omni PCB's Buried and Blind Vias are manufactured using the latest technology to ensure high efficiency and optimal performance. Unlike traditional PCBs, these vias are ideal for compact designs and reduce signal loss while providing better communication. The company's advanced technology and skilled team make it possible for them to produce high-quality Buried And Blind Vias that meet stringent industry standards. With state-of-the-art facilities, they manufacture PCBs with intricate designs that meet even the most demanding requirements.The advantage of Buried and Blind Vias lies in its ability to connect different layers of a PCB without appearing on the surface. This technology increases the density of components and reduces layer counts, enabling routing in tight areas where it would otherwise be impossible. Buried Vias are drilled from the inner layers and terminate inside the board, while Blind Vias are drilled from the surface and terminate at a specified depth within the board, allowing for the creation of multiple layers of routing without the need for additional space.The company takes pride in providing its customers with high-quality PCB solutions to meet their needs and is committed to meeting the unique requirements of every client. Their attention to quality sets them apart from other PCB assembly companies, as their products are inspected throughout the production process to ensure that only high-quality PCBs are delivered to their clients.In addition to its commitment to quality, Omni PCB has also optimized its manufacturing processes to ensure that customers receive their products faster and at a competitive price. This combination of quality, efficiency, and competitive pricing makes them a leading manufacturer, supplier, and factory of Buried and Blind Vias in China.As an industry leader, Omni PCB has introduced the latest technology and innovations in PCB design, ensuring that their team of skilled professionals is committed to delivering products that meet the needs of their clients. With Buried and Blind Vias, clients can trust the company's services to provide top-of-the-line solutions that will help them achieve their goals in the most efficient and cost-effective way possible.The testimonials from industry experts further strengthen the company's reputation, as Ms. Carlen Shu emphasizes the crucial role of buried and blind vias as an essential feature of modern printed circuit boards. She highlights their efficient design, reliable connectivity, and superior electrical performance, making them an indispensable technology for modern-day electronics. Ms. Angela Her emphasizes the game-changing nature of buried and blind vias technology in high-performance PCB manufacturing, ensuring greater reliability and functionality without the need for more space.With a strong track record in the industry, Omni PCB is dedicated to providing superior quality PCB products, including Buried and Blind Vias, to meet the diverse needs of its clients. Their commitment to quality, efficiency, and innovation positions them as a leading manufacturer and supplier of high-quality PCB solutions in China. Clients can rely on Omni PCB for top-quality products, efficient manufacturing processes, and exceptional customer service to meet their PCB requirements.
Explore Flexible PCB Solutions for Your Circuit Board Needs on icape-shop.com
Rigid-Flex PCB Technology Continues to Reach New Heights with ICAPE Group's SolutionsThe world of electronics is constantly evolving, with new technology and innovations emerging all the time. One of the most exciting developments in recent years has been the rise of rigid-flex printed circuit boards (PCBs). These PCBs are a hybrid of both rigid and flexible PCB technologies, allowing for more flexible designs and greater functionality in electronic devices.As one of the leading providers of printed circuit board solutions, the ICAPE Group is at the forefront of the rigid-flex PCB revolution. With a wide range of cutting-edge solutions for flexible PCBs, ICAPE is helping companies across a range of industries take advantage of this powerful technology.Whether you're looking to create a highly complex electronic device or a simple, streamlined product, flexible PCBs can provide the design versatility and functionality you need. With flexible PCBs, the circuits are mounted on top of a flexible substrate, rather than a rigid board. This allows the PCB to bend and flex, which can be particularly useful in applications where space is limited or where the board may be subjected to high levels of vibration or other stresses.One of the key benefits of flexible PCBs is their ability to improve reliability and reduce failure rates. Because they can be designed to fit the exact needs of a particular application, they can also be more reliable over the long term. Additionally, because they can be constructed with fewer parts than traditional PCBs, they are often less prone to failure.At ICAPE, we offer a range of solutions for flexible PCBs that can be customized to meet the specific needs of your application. Our expert engineers can work closely with you to develop a design that meets your exact requirements, ensuring that you get the best possible results.Our flexible PCBs are available in a range of materials, including copper, polyester, and thermoplastics. We can also provide a range of different levels of flexibility, making it possible to create a PCB that can bend and flex to a high degree or one that is more rigid and stable.In addition to our flexible PCB solutions, we also offer a range of other printed circuit board solutions to suit your needs. These include standard and complex multilayer PCBs, as well as specialized boards for high-frequency applications and more.At ICAPE, our focus is on providing our customers with the highest quality printed circuit board solutions that can help them succeed in a rapidly changing and highly competitive market. Whether you're looking for flexible PCBs, rigid PCBs, or any other type of PCB solution, we have the expertise and experience needed to deliver the results you need.If you're interested in learning more about our flexible PCB solutions, please visit our e-shop at www.icape-shop.com. We would be happy to answer any questions you may have and help you find the perfect solution for your needs.
Affordable Low Cost PCB Prototype from Chinese Manufacturer, Supplier, Factory
Low Cost PCB Prototype Service Offers High-Quality Products at Affordable Prices"With an experience of over 30 years old, a seasoned manufacturer of Printed Circuit Boards has been offering state-of-the-art PCBs. The company, known for its commitment to quality and efficient turnaround times, has recently launched a low-cost PCB prototype service to cater to DIY electronics enthusiasts, startups, and established companies looking to design and test new circuits.The low-cost PCB prototype service is the perfect solution for those who need a high-quality printed circuit board at an affordable price. With the company's state-of-the-art facility and experienced technical team, customers can be confident in receiving PCB prototypes that meet their exact specifications.One of the key factors that set the company apart from other PCB suppliers is its unwavering commitment to quality. The PCB products undergo rigorous inspections throughout the production process, including PCB designing, assembly, and 3D PCB printing, ensuring that only high-quality products are delivered to customers.Utilizing advanced technology and quality materials, the company ensures that its products not only meet but exceed customers' expectations. This attention to detail and commitment to quality make the company a reliable choice for those seeking cost-effective PCB prototyping.The company's low-cost PCB prototype service is designed to meet the unique needs of each project. Customers can expect excellent customer service from start to finish, with the company's technical team available for consultation at every step of the process.In addition to delivering high-quality products, the company also prides itself on its fast turnaround times. Customers can expect their prototype to be delivered promptly, allowing them to move forward with their projects without any delay.The launch of this low-cost PCB prototype service is a testament to the company's dedication to providing innovative solutions that meet the needs of customers across various industries. By offering affordable PCB prototypes without compromising on quality, the company aims to support the development of new and groundbreaking technologies.This new service particularly benefits those in the electronics industry who rely on reliable prototypes before moving towards full-scale production. By providing cost-effective solutions, the company is helping to bridge the gap between innovation and affordability in the electronics sector.With its extensive experience and commitment to quality, this seasoned manufacturer of Printed Circuit Boards in China is well-positioned to meet the increasing demands for low-cost PCB prototypes in the market.In conclusion, for those in need of a reliable PCB prototype service that won't break the bank, this company's low-cost PCB prototype service is the perfect solution. With its focus on quality, affordability, and quick turnaround times, customers can trust the company to deliver products that meet their specifications and exceed their expectations. Contact the company today to take advantage of the affordable PCB prototype service and bring innovative ideas to life.
High-Quality PCB Assembly Services for the Electronics Industry: Full Turn-Key and Partial Turn-Key Available
, Quality PCB Assembly, and Turn-Key PCB Assembly.Are you looking for a reliable and affordable PCB assembly service provider? Look no further than Rayming – a leading provider of full Turn-Key and partial Turn-Key PCB Circuit Board Assembly Services.At Rayming, we understand that every project is unique and requires a tailored assembly solution. That’s why we offer both rigid PCB assembly and flex PCB assembly services to meet your specific needs. Our quality policy driven PCB assembly process ensures that your projects meet the highest standards of quality.In Full Turn-Key PCB assembly, we provide end-to-end solutions – from PCB fabrication to component procurement, PCB assembly, and testing – all under one roof. This ensures that you get a hassle-free experience and save time and money in the process.We also offer partial Turn-Key PCB assembly services where you provide the PCBs and some of the components while we source and assemble the remaining components.At Rayming, our team of skilled technicians has years of experience in PCB assembly and uses the latest equipment and techniques to ensure the highest quality output. We specialize in LED PCB assembly, automotive PCB assembly, medical device PCB assembly, and much more.What’s more, we understand that you need your PCBs delivered on time and within budget. That’s why we have a strict delivery schedule and offer affordable rates without compromising on quality.So if you are looking for cheap PCB assembly services without compromising on quality, look no further than Rayming. Contact us today to learn more about our Full Turn-Key, Partial Turn-Key, and Flex PCB assembly services.
Top Electronics Suppliers in China - Reliable Manufacturer, Supplier, and Factory
Leading Electronics Suppliers Offer Cutting-Edge Products and Reliable ServicesThe demand for high-quality electronic products continues to grow rapidly, and consumers are always on the lookout for reliable suppliers who can deliver top-notch technology at affordable prices. In today's digital age, finding a trustworthy electronics supplier is essential for both personal and professional needs.One company that has made a mark in the electronics supply industry is a seasoned manufacturer of Printed Circuit Boards (PCBs) with over 30 years of experience. This company, known for their state-of-the-art PCBs, has refined their processes to ensure they can offer the highest quality PCB products in the shortest possible time.Quality is a crucial factor for electronics suppliers, and this company prides itself on delivering products that meet industry standards. With a strong focus on customer satisfaction, they ensure that their PCBs undergo rigorous testing procedures at every stage of production, including designing, assembly, and 3D printing. This commitment to excellence sets them apart from other suppliers and ensures that their products are durable and long-lasting.The company's dedication to quality and customer satisfaction is aligned with their mission to provide an enjoyable and hassle-free shopping experience for their customers. Their user-friendly website makes it easy for customers to browse and purchase products from the comfort of their homes, ensuring that they have access to the best electronics suppliers in the market.In addition to their focus on quality, this company also values timely delivery and customer service. They understand the importance of delivering products as agreed upon and as early as possible, ensuring that their customers can rely on them for their electronic needs.On the other hand, in the world of cutting-edge electronics, another leading manufacturer, supplier, and factory based in China, offers a wide range of electronic products including mobile phones, laptops, speakers, headphones, and much more. Their commitment to excellence and customer satisfaction sets them apart from other electronics suppliers in the market. With the use of the latest technology and manufacturing processes, they ensure that their products are of the highest quality while remaining affordable and accessible to everyone.For consumers who are looking to purchase electronic devices for their personal or professional needs, the feedback from satisfied customers is a testament to the quality of products and services offered by this leading electronics supplier. Customers have reported positive experiences with their purchases, highlighting the sleek, lightweight, and durable nature of the electronic devices, as well as the prompt delivery and reasonable pricing.Moreover, the company's focus on customer service and knowledgeable sales staff sets them apart from others in the industry. Their competitive prices, great deals, and promotions also make them a top choice for consumers in need of any electronic device.As technology continues to evolve, consumers are constantly seeking innovative and efficient electronic products. Therefore, with a strong focus on quality, reliability, and customer satisfaction, both the mentioned electronics suppliers are dedicated to meeting the ever-changing needs of the market and providing cutting-edge technology to consumers worldwide.In conclusion, as the demand for electronic products continues to rise, it is essential for consumers to have access to reliable and high-quality electronics suppliers. Both the seasoned manufacturer of Printed Circuit Boards and the leading electronics supplier in China are committed to providing top-notch products, reliable services, and a seamless shopping experience for their customers. With a strong focus on quality, timely delivery, and customer satisfaction, these companies have earned a reputation as top electronics suppliers in the market, meeting the ever-changing needs of consumers and businesses worldwide.
High-quality LED Metal Core Printed Circuit Board for Efficient Lighting System
In today's world, LED technology has become an essential part of our daily lives. From the streetlights to the smartphones, LED technology has transformed the way we see the world. Recently, Woeufu has introduced an innovative LED MCPCB that is changing the game for the LED industry.Woeufu is a leading company in the electronics industry that focuses on manufacturing high-quality electronic components. With over 15 years of experience, the company has been able to establish a strong foothold in the market by delivering high-quality products at competitive prices. Woeufu has a team of highly experienced engineers who specialize in designing innovative electronic products that cater to the needs of various industries.One of the latest products from Woeufu is their LED MCPCB (Metal Core Printed Circuit Board). The MCPCB has a unique design that allows it to efficiently dissipate heat generated by the LEDs. The MCPCB is made of a metal core, which acts as a heat sink, reducing the temperature of the LEDs and increasing their lifespan.The LED MCPCB by Woeufu is designed for 16 LEDs and comes in sets of four, with each set consisting of four LEDs. The MCPCB is designed to run at 12V, making it suitable for a wide range of applications. The MCPCB is perfect for applications that require a high amount of light output while keeping the temperature of the LEDs under control.The LED MCPCB by Woeufu is easy to install and can be used in a variety of applications. It is ideal for use in LED streetlights, high-bay lights, and floodlights. The MCPCB is also suitable for use in automotive lighting, such as headlights and taillights, where heat dissipation is essential for longevity.According to Woeufu, their LED MCPCB is designed to be highly efficient, with a low thermal resistance of 0.12℃/W. This means that the MCPCB can dissipate heat quickly, ensuring that the LEDs remain cool and have a longer lifespan. The MCPCB also has a high thermal conductivity of 1.6W/mK, which further helps in the efficient dissipation of heat.The LED MCPCB by Woeufu is manufactured using high-quality materials and is subjected to rigorous testing to ensure that it meets the highest standards of quality. The MCPCB is designed to withstand extreme temperatures, making it suitable for use in harsh environments.In conclusion, the LED MCPCB by Woeufu is a game-changer for the LED industry. It offers a unique solution to the heat dissipation problem that has plagued the industry for years. With its innovative design and high-quality construction, the LED MCPCB is perfect for a wide range of applications where efficient heat dissipation is essential. Thanks to Woeufu's dedication to quality and innovation, the LED MCPCB is set to become the go-to solution for LED lighting applications in the future.
Step-by-Step Guide to Creating a 4-Layer PCB
In today's digital age, technology has become an integral part of our daily lives. One of the most breakthroughs in technology is printed circuit board (PCB) designing. PCBs are the foundation of almost all electronic devices, from smartphones to laptops – you name it. A high-performance and reliable PCB should be well-designed and manufactured, or else it could lead to catastrophic consequences. To achieve a high-quality PCB, the 4-layer PCB is at the forefront.But what is a 4-layer PCB? Simply put, it has four layers of copper traces separated by an insulating layer, also known as a dielectric layer. Unlike its 2-layered counterpart, a 4-layer PCB offers a myriad of benefits. It enables a higher density of components, provides better and more stable signal integrity, allows for easier implementation of ground planes, and has a lower electromagnetic interference (EMI) and crosstalk. As a result, 4-layer PCBs are widely used in complex electronic systems, especially in high-speed communication applications.So, what is the process to make a 4-layer PCB? The first step is to start with the layout design. The designer uses PCB design software to create a schematic diagram, which is then translated into a physical design layout. Once this is done, the designer must choose a suitable substrate material – commonly FR-4 – and determine the thickness of the copper foil required.Next, the designer creates a drill template for each layer, which determines the location of the holes that will be drilled throughout the board. The board is then laminated together with adhesive, and the copper foil is etched away to create the layer's traces. An automated machine drills holes through the board at the specified locations, and the inner layers are aligned to the drill holes and laminated onto the previously assembled layers.Once the layers are assembled, the board is plated using electroplating, and a solder mask is added to provide insulation and protection to the copper traces. Lastly, the board is silk screened with the component placement legend, a code that displays each component's location and orientation.As the demand for technological devices continues to rise, the development of high-quality and reliable PCBs like the 4-layer PCB is crucial. In this regard, several manufacturers are investing in the development of advanced PCBs. One such company that has found considerable success in PCB design and manufacturing is [company name here].[Company name here] specializes in the design and production of high-quality PCBs that meet the demands of various industries. With years of experience in the industry, the company has been able to build an exceptional portfolio of solutions that cater to their clients' needs. They offer a wide range of PCB designs, including the 4-layer PCB.One of the company's unique features is their expertise in utilizing advanced software to design their PCBs, streamlining the entire manufacturing process, from design to production, and ensuring that their products adhere to the highest quality standards. Their deep knowledge on the various materials used for different types of PCBs has also placed them in a unique position to advise their customers on choosing the right materials for their projects.In conclusion, for most electronic devices, the PCB is the backbone, and as such, the demand for high-quality PCB design and manufacturing will continue to rise. The 4-layer PCB stands out as an excellent option for high-performance electronic systems, where reliability and stability are paramount. [Company name here] is an industry leader in PCB design and manufacturing, offering top-of-the-line solutions suited for varying industries.
Top Circuit Board Manufacturer Shares Key Insights for Enhanced Electronics Production
Omni Circuit Boards Expands its Presence in the Electronics Manufacturing IndustryOmni Circuit Boards, a leading provider of high-quality printed circuit boards (PCBs), is making waves in the electronics manufacturing industry with its commitment to exceptional customer service and innovative board solutions. With its relentless pursuit of excellence, Omni Circuit Boards has solidified its position as a trusted partner for businesses across various sectors.Since its inception, Omni Circuit Boards has been at the forefront of PCB manufacturing, catering to both small-scale projects and large-scale industrial applications. The company's extensive experience, coupled with its state-of-the-art facilities and cutting-edge technology, has enabled it to produce reliable and efficient circuit boards that meet the stringent demands of the industry.One of the key factors that sets Omni Circuit Boards apart from its competitors is its unwavering focus on customer satisfaction. Regardless of the project size or complexity, the company's team of highly skilled engineers and technicians work closely with clients to understand their specific requirements and provide tailored solutions. This commitment to personalized service has earned Omni Circuit Boards a loyal customer base that spans multiple industries, including aerospace, automotive, medical, telecommunications, and more.In addition to its customer-centric approach, Omni Circuit Boards boasts a technologically advanced manufacturing facility equipped with the latest equipment and tools. The company continually invests in upgrading its infrastructure to deliver best-in-class PCBs that meet the evolving needs of the industry. From single-layer boards to multi-layer designs, Omni Circuit Boards has the expertise and capability to handle a wide range of projects with precision and efficiency.Furthermore, the company places a strong emphasis on quality control throughout the entire manufacturing process. Stringent quality checks are conducted at every stage, starting from the initial design and layout to the final inspection, ensuring that each PCB meets the highest industry standards. By adhering to rigorous quality control procedures, Omni Circuit Boards guarantees that its products are reliable, durable, and perform optimally in the most demanding operational environments.In a rapidly evolving industry, Omni Circuit Boards stays ahead of the curve by keeping a pulse on the latest technological advancements. The company invests heavily in research and development to explore innovative PCB manufacturing techniques and materials. By staying at the forefront of technological advancements, Omni Circuit Boards consistently delivers cutting-edge solutions that provide a competitive edge to its clients.Furthermore, Omni Circuit Boards understands the importance of environmental sustainability in today's world. The company actively promotes eco-friendly practices throughout its operations. Special consideration is given to reducing waste, optimizing energy consumption, and eliminating harmful substances in its manufacturing processes. This commitment to environmental responsibility not only benefits the planet but also aligns with the values of many of the company's environmentally conscious clients.As Omni Circuit Boards continues to expand its reach in the electronics manufacturing industry, it remains steadfast in its dedication to customer satisfaction, technological innovation, and environmental sustainability. With a track record of excellence and a commitment to staying at the forefront of the industry, the company is well-positioned to meet the evolving needs of its clients and maintain its position as a trusted leader in the PCB manufacturing sector.In conclusion, Omni Circuit Boards' continuous growth and success can be attributed to its customer-centric approach, relentless pursuit of excellence, and commitment to technological innovation. With its state-of-the-art facilities, cutting-edge technology, and highly skilled team, the company sets the benchmark for PCB manufacturing. As it continues to expand its presence, Omni Circuit Boards is poised to play a vital role in shaping the future of the electronics manufacturing industry.
Understanding the Importance of PCBs in Medical Devices: A Guide
The medical field is constantly adapting and evolving, and one of the latest innovations making waves in the industry is Pcb Medical Meaning. This cutting-edge technology is set to revolutionize the way medical professionals diagnose and treat patients, offering a myriad of benefits and advancements that could significantly improve healthcare outcomes.Pcb Medical Meaning, developed by {}, is a sophisticated medical device that utilizes advanced imaging technology to provide a more accurate and detailed picture of the body's internal structures. This device has the potential to streamline the diagnostic process, enabling healthcare providers to make more informed decisions regarding patient care.This innovative technology is designed to be versatile and adaptable, with the capability to be used in a variety of medical specialties. From radiology to cardiology, Pcb Medical Meaning has the potential to enhance the way medical professionals approach and address a wide range of health conditions.In addition to its diagnostic capabilities, Pcb Medical Meaning also promises to improve patient comfort and safety. With its high-resolution imaging and precise data, this technology can reduce the need for invasive procedures and minimize patient exposure to radiation. This could ultimately lead to better patient experiences and outcomes.Furthermore, Pcb Medical Meaning has the potential to empower medical professionals to provide more personalized and targeted treatments. By offering a comprehensive and detailed view of a patient's condition, this technology can help doctors develop more tailored and effective treatment plans, ultimately leading to better health outcomes for their patients.{} has been at the forefront of medical innovation for over a decade, consistently pushing the boundaries of what is possible in the field of healthcare technology. With a focus on research and development, the company has a track record of producing cutting-edge medical devices that improve patient care and streamline healthcare processes.The company's dedication to innovation and excellence has earned them a reputation as a leader in the medical technology industry. With a team of highly skilled engineers, researchers, and medical professionals, {} is committed to developing groundbreaking solutions that address the evolving needs of the healthcare industry.In addition to their technical expertise, {} is also known for their commitment to ethical and responsible business practices. The company prioritizes safety, quality, and compliance in all of their products, ensuring that their technology meets the highest standards of performance and reliability.By combining their technical prowess with a dedication to improving patient care, {} has positioned themselves as a key player in the medical technology market. With the introduction of Pcb Medical Meaning, the company is once again demonstrating their commitment to advancing the field of healthcare and improving the lives of patients worldwide.In conclusion, Pcb Medical Meaning, developed by {}, represents a significant advancement in medical technology that has the potential to transform patient care and healthcare processes. With its advanced imaging capabilities, versatile applications, and focus on patient comfort and safety, this innovative technology promises to have a profound impact on the way medical professionals diagnose and treat a wide range of health conditions. As a leader in the medical technology industry, {} is well-positioned to drive the adoption and integration of Pcb Medical Meaning into healthcare systems around the world, ultimately leading to improved patient outcomes and a more effective and efficient healthcare system.