Step-by-Step Guide to Creating a 4-Layer PCB
By:admin
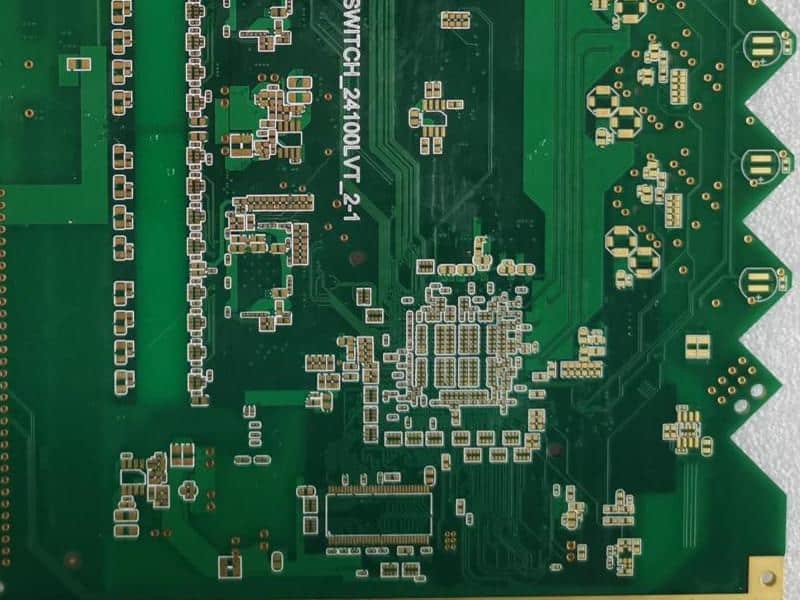
But what is a 4-layer PCB? Simply put, it has four layers of copper traces separated by an insulating layer, also known as a dielectric layer. Unlike its 2-layered counterpart, a 4-layer PCB offers a myriad of benefits. It enables a higher density of components, provides better and more stable signal integrity, allows for easier implementation of ground planes, and has a lower electromagnetic interference (EMI) and crosstalk. As a result, 4-layer PCBs are widely used in complex electronic systems, especially in high-speed communication applications.
So, what is the process to make a 4-layer PCB? The first step is to start with the layout design. The designer uses PCB design software to create a schematic diagram, which is then translated into a physical design layout. Once this is done, the designer must choose a suitable substrate material – commonly FR-4 – and determine the thickness of the copper foil required.
Next, the designer creates a drill template for each layer, which determines the location of the holes that will be drilled throughout the board. The board is then laminated together with adhesive, and the copper foil is etched away to create the layer's traces. An automated machine drills holes through the board at the specified locations, and the inner layers are aligned to the drill holes and laminated onto the previously assembled layers.
Once the layers are assembled, the board is plated using electroplating, and a solder mask is added to provide insulation and protection to the copper traces. Lastly, the board is silk screened with the component placement legend, a code that displays each component's location and orientation.
As the demand for technological devices continues to rise, the development of high-quality and reliable PCBs like the 4-layer PCB is crucial. In this regard, several manufacturers are investing in the development of advanced PCBs. One such company that has found considerable success in PCB design and manufacturing is [company name here].
[Company name here] specializes in the design and production of high-quality PCBs that meet the demands of various industries. With years of experience in the industry, the company has been able to build an exceptional portfolio of solutions that cater to their clients' needs. They offer a wide range of PCB designs, including the 4-layer PCB.
One of the company's unique features is their expertise in utilizing advanced software to design their PCBs, streamlining the entire manufacturing process, from design to production, and ensuring that their products adhere to the highest quality standards. Their deep knowledge on the various materials used for different types of PCBs has also placed them in a unique position to advise their customers on choosing the right materials for their projects.
In conclusion, for most electronic devices, the PCB is the backbone, and as such, the demand for high-quality PCB design and manufacturing will continue to rise. The 4-layer PCB stands out as an excellent option for high-performance electronic systems, where reliability and stability are paramount. [Company name here] is an industry leader in PCB design and manufacturing, offering top-of-the-line solutions suited for varying industries.
Company News & Blog
Close-up of Components on a Printed Circuit Board (PCB) - High-Quality Stock Image
A printed circuit board (PCB), also known as a circuit board, is an essential component of any electronic device, whether it's a smartphone, a laptop, a television, or any other gadget. PCBs come in different shapes and sizes depending on the specific device’s design and function, but all serve the same purpose: to provide a platform for connecting various electronic components.A PCB is essentially a thin board made of insulating material (such as fiberglass or plastic) with a conductive layer printed on it. The conductive layer is usually made of copper, which is etched to create pathways (or traces) that connect different components. These components may include resistors, capacitors, diodes, transistors, and integrated circuits.Circuit boards are the backbone of modern electronics, and they’re becoming increasingly important as technology continues to evolve. They allow electronic devices to be smaller, lighter, and more efficient while providing more functionality. Without them, many of the devices we rely on today would not be possible.The design of a PCB is critical to its functionality and performance. The layout and spacing of components must be carefully planned to ensure that they don't interfere with each other and that the circuit operates correctly. Software tools are used to create PCB designs that allow engineers to simulate the circuit's behavior and optimize its performance.Once the PCB design is complete, the board is manufactured using specialized equipment that prints the conductive layer onto the insulating material and etches away the excess copper. The boards are then inspected for quality and tested to ensure that they function as designed.PCBs are used in a wide range of applications, from consumer electronics to industrial machinery. They’re also used in medical devices, aerospace components, and automotive systems. The automotive industry, in particular, relies heavily on PCBs for things like engine control units, airbag sensors, and entertainment systems.In conclusion, PCBs are a critical component of modern electronics and play a crucial role in the functionality and performance of electronic devices. They allow for smaller, more efficient devices with more advanced features. The design and manufacturing of PCBs require specialized skills, making them an important part of the electronics industry. As technology continues to evolve, PCBs will continue to play a crucial role in the development of new and innovative products.
Get Rapid Prototyping and Fast Delivery for PCBs with Quick Turn Services
: The Importance of Timely DeliveryIn today's fast-paced world, where technological advancements are happening at an unprecedented rate, Quick Turn Printed Circuit Boards (PCBs) have emerged as a game-changer. These PCBs are capable of speeding up the production process and helping businesses meet their deadlines. With a growing demand for PCBs, it has become imperative for manufacturers to deliver them on time to remain competitive in the market.In this blog post, we will discuss the importance of timely delivery of Quick Turn PCBs and why it is critical for businesses to choose a reliable and trusted supplier for their PCB needs.Meeting DeadlinesDeadlines are crucial for businesses, and delays in delivery can result in significant losses both in terms of time and money. PCBs are an essential component in many industries, including automotive, medical, aerospace, and telecommunications, among others. Ensuring timely delivery of these PCBs can be the difference between meeting customer expectations and losing business to competitors. Therefore, choosing a supplier who can deliver custom-made PCBs quickly and efficiently is fundamental.Reducing CostsManufacturers can incur additional costs if the PCBs are not delivered on time. For example, if the delivery of PCBs is delayed, the company might need to switch to air freight, which can be expensive. Additionally, any missed deadlines or late deliveries can lead to production downtime, staff overtime payments, and a loss of revenue. Therefore, timely delivery of Quick Turn Printed Circuit Boards can help businesses save costs and stay competitive in the market.Maintaining Quality StandardsQuick Turn PCBs are designed and manufactured at a rapid pace. Therefore, it is essential to ensure that the quality of these PCBs is not compromised in the process. A reliable and trustworthy supplier will guarantee that the PCBs meet industry standards and quality requirements, ensuring customer satisfaction. This ultimately leads to repeat business and more significant opportunities for growth and expansion.Choosing the Right SupplierChoosing the right PCB supplier is crucial to ensure timely delivery of Quick Turn PCBs. A reliable and quality supplier will have a streamlined production process in place, ensuring faster delivery times. They will also employ highly skilled and experienced personnel to manufacture Printed Circuit Boards and perform quality control checks to ensure the PCBs meet industry standards.ConclusionIn today's ever-changing and demanding marketplace, timely delivery of Quick Turn Printed Circuit Boards is crucial for businesses to meet customer expectations and stay ahead of the competition. Therefore, it is essential to choose a reliable supplier who can guarantee on-time delivery, maintain quality standards, and provide cost-effective solutions for your PCB needs.At WonderfulPCB, we are committed to providing exceptional services to our clients by delivering Quick Turn PCBs within a short duration and ensuring quality standards are met. Contact us today for all your PCB requirements, and we will be happy to help you meet your deadlines and ensure business success.
PCB Assembly Solderability Validation Tests Ensure High-Quality Standards
ATP's PCB Assembly Solderability Validation Tests: Ensuring the Highest Standards of QualityThe reliability and endurance of printed circuit board assemblies (PCBAs) are critical factors that determine their overall performance. Defective PCBs can disrupt entire systems and negatively impact product functionalities. That's why PCB assembly validation tests are vital in ensuring that the PCBAs meet the highest quality standards. ATP is a renowned company that specializes in delivering reliable and high-performance PCB assemblies. One of their crucial tests is the PCB Assembly Solderability Validation Test.PCB Assembly Solderability Validation TestThe solderability of a PCB refers to its ability to form a durable and strong bond with the intended components through the soldering process. Various factors can affect the performance of the solder joints, including oxidation, moisture, and contamination. PCB Assembly Solderability Validation Test is an essential test that aims to evaluate the soldering capability of the PCB. Additionally, this test confirms that the PCBs are free of contamination, oxidation, or any other factors that could hinder the formation of a strong bond.The Test ProcessThe PCB Assembly Solderability Validation Test process starts by identifying the critical components of the PCB assembly. The process evaluates the adhesion and compatibility of the components with the PCB by exposing them to environmental conditions that could potentially affect their performance. After evaluating the components, the PCB goes through a series of tests to confirm that the assembly process meets the industry standards.The test process involves using solder paste and reflow soldering to evaluate the quality of the PCBAs. The PCB is heated to a specific temperature, and the solder paste is applied to the board's surface. The solder forms a strong bond with the PCB, making it possible to attach various components to the PCB. The tests evaluate the solderability aspect of the PCB, which is an essential factor for the assembly's overall quality.Testing StandardsThe PCB Assembly Solderability Validation Test follows various industry standards, including the IPC J-STD-001, which outlines the requirements for the quality and reliability of soldered electrical and electronic assemblies. The test protocols ensure that all components are adequately and thoroughly inspected, including the electrical connections, surface mount components, and through-hole components. Additionally, this test confirms that the assemblies comply with the industry standards for surface finish, hole filling, and component alignment.Benefits of the PCB Assembly Solderability Validation TestThe PCB Assembly Solderability Validation Test ensures that the PCBs are free from defects that could compromise their performance. The test leads to a significant reduction in the risk of product failure and increases the overall reliability of the PCB assembly. Additionally, the test ensures that the PCBs meet the highest quality standards set by the industry, which is crucial in meeting the customer's expectations.ConclusionATP is committed to delivering high-quality PCB assemblies that meet the highest standards of quality and reliability. The PCB Assembly Solderability Validation Test is an essential part of the many reliability and endurance tests developed and performed by ATP to ensure strict compliance with the highest quality standards. The test ensures that the PCBs are free from defects that could potentially compromise their performance and overall reliability. By using the latest testing standards, ATP ensures the optimal quality of the PCB assemblies to meet the customer's expectations.
A Comprehensive Guide to Selecting MCPCB for Compatible LED Mounting Bases with Enhanced Performance
Title: Choosing the Perfect MCPCB Compatible with CREE LEDsIntroduction:When it comes to ensuring efficient and long-lasting LED lighting solutions, the selection of the right materials and components is paramount. MCPCB, or Metal Core Printed Circuit Board, is a crucial element that significantly impacts the performance and functionality of LED modules. In this blog post, we will explore the importance of choosing the perfect MCPCB compatible with CREE LEDs, without mentioning any specific brand name, and discuss how custom MCPCBs can enhance your LED lighting solutions.What is MCPCB and its Role in LED Modules?MCPCB is a specialized circuit board with a metal core, typically made of aluminum or copper. It is specifically designed to support high-power LEDs and other heat-generating components by effectively dissipating heat, ensuring optimal thermal management. The metal core acts as a heat sink, efficiently transferring the heat away from the LED junction, ultimately improving the overall performance, luminous efficacy, and lifespan of the LED module.Why Compatibility with CREE LEDs Matters:CREE is globally recognized as a leading manufacturer of high-performance LEDs, renowned for their exceptional brightness, color accuracy, and energy efficiency. As such, selecting MCPCBs compatible with CREE LEDs is crucial to fully utilize and enhance these superior LED products' capabilities. Compatibility ensures optimized heat dissipation, thereby preventing the LED from reaching high temperatures that can negatively impact its performance, reliability, and lifespan.Benefits of Custom MCPCBs:When it comes to selecting MCPCBs for LED modules, custom solutions offer a range of advantages tailored to your specific lighting requirements. Let's explore some benefits of opting for custom MCPCBs:1. Efficient Heat Dissipation: Custom MCPCBs are designed to optimize heat dissipation specifically for the LED module's requirements and the operating environment. This ensures effective cooling, preventing overheating and maintaining consistent performance in even the harshest conditions.2. Enhanced Durability: By customizing the MCPCB, you can choose materials with enhanced durability and resistance to environmental factors such as moisture, corrosion, and vibration. This improves reliability and extends the lifespan of your LED modules.3. Flexibility in Design: Custom MCPCBs offer design flexibility, allowing you to tailor the circuit board to fit various shapes, sizes, and layouts of LED modules. This makes it easier to integrate lighting solutions into different applications while maintaining optimal thermal management.4. Precise Circuit Traces and Wiring: Opting for custom MCPCBs enables precise positioning of circuit traces and wiring, ensuring efficient electrical performance and minimizing power loss. This enhances the overall efficiency and reliability of the LED module.5. Cost-Effective: While custom solutions may initially seem more expensive, they often prove to be cost-effective in the long run. Custom MCPCBs efficiently dissipate heat, which reduces the need for additional cooling mechanisms, such as fans or heat sinks. This lowers maintenance costs and energy consumption while maximizing the LED module's performance.Conclusion:Selecting the perfect MCPCB compatible with CREE LEDs is vital for maximizing the performance, efficiency, and lifespan of your LED lighting solutions. By choosing custom MCPCBs, you can optimize heat dissipation, enhance durability, and enjoy design flexibility tailored specifically to your LED module requirements. This not only ensures superior lighting performance but also proves to be a cost-effective investment in the long run. Invest in custom MCPCBs to unlock the full potential of your CREE LEDs and deliver exceptional lighting experiences across various applications.
China-based Manufacturer Offers HDI PCB Manufacturing and SMT PCB Assembly Services
The world is constantly changing, and with each passing day, technology advancements are hitting the market leaving no industry untouched. The world of printed circuit boards is no exception to the rapid change and development. These circuit boards are becoming increasingly popular in the electronics industry for their ability to offer greater flexibility, reliability, and precision.Of all the PCB types that exist, HDI PCB is a game-changer in terms of technological advancement. HDI stands for High-Density Interconnect PCBs. An HDI PCB board is designed and structured to increase the density of electronic interconnects on a circuit board by reducing the size of the components. The size of electronic components and their spacing is an essential factor during the design and manufacturing process of HDI PCB boards.At Heros Electronics (alternative name), we specialize in manufacturing and assembling high-quality HDI PCBs to meet the ever-growing demands of the electronics industry. Here, we provide a wide range of high-end solutions to help our customers satisfy their requirements.Why Choose HDI PCB Board Manufacturing with Heros Electronics?HDI PCBs manufactured and assembled at Heros Electronics are optimized for cost-effectiveness, reliability, flexibility, and performance. Our team of experts uses the latest technology, a thorough quality control process, and a dedicated approach to develop and deliver high-quality HDI PCB boards. Here are a few reasons to choose HDI PCB board manufacturing with Heros Electronics:1. Better Density:HDI PCB boards have a higher component density in comparison to traditional or standard circuit boards. This increase in the number of components and the reduction in the size of components help reduce the circuit board's size and weight. Due to the high component density, HDI PCBs can carry out complicated tasks even in limited space.Our HDI PCB board manufacturing capabilities allows us to produce small and lightweight PCB boards without compromising performance.2. Improved Performance:HDI PCBs are designed in a way that reduces the distance between different components, which in turn, improves the signal transmission capability of the circuit board. This reduction of the signal path leads to decreased noise interference and better electrical performance. The short interconnect paths of HDI PCB can also lower resistance and electrical losses, further improving the overall functionality and design of your printed circuit board.3. Cost-Effective Solution:Despite being advanced technology, our HDI PCB board manufacturing process helps us provide cost-effective solutions to our customers. Advanced manufacturing techniques, component sourcing, PCB assembly, and extensive testing help to reduce the overall costs associated with an HDI PCB board development project. At Heros Electronics, we offer competitive pricing without compromising quality.4. Customization:At Heros Electronics, we understand that every customer has unique needs, requirements, and specifications; therefore, we work with our customers to develop customized HDI PCBs for their specific applications. Our engineering team evaluates each aspect of the customer project and provides a range of solutions to meet all their electronic needs.5. Quick Delivery:We value our customers’ time and understand how crucial timely project completion is. Therefore, we always strive to deliver our HDI PCB boards on time without compromising the quality of the product. Our experts are well-trained to handle orders of various sizes and complexities.Conclusion:HDI PCB boards are becoming increasingly popular in the electronics industry due to its various benefits. At Heros Electronics, we specialize in HDI PCB board manufacturing and assembly using cutting-edge technology and sophisticated techniques. We understand how important it is to meet all of our customer’s needs promptly, affordably, and with the highest level of quality. Contact us today to experience our hassle-free services and take advantage of our experience and expertise in developing, manufacturing, and delivering high-quality HDI PCB board solutions.
Freelance Electronics Engineer Needed for 60x30mm PCB Board to Connect Battery and Camera for Phone Recording via Wi-Fi/Bluetooth
, Battery and Camera Connection, Wi-Fi, Bluetooth, and Product Design.As technology continues to advance, portable devices have become more popular than ever before. From smartphones to tablets, the ability to connect with others and capture life's moments has never been easier. This is why there is an increased demand for printed circuit board (PCB) design, product design, and electrical engineering projects that enable users to record and connect their devices seamlessly. One example of a recent project in this field is the creation of a 60mm x 30mm PCB board that connects a battery and camera to a phone over Wi-Fi or Bluetooth connection. This project was designed to meet the growing demand for portable, easy-to-use recording devices that can be used on the go.PCB Board Layout: The First Step to Creating Better ProductsPCB board layout is one of the most crucial parts of creating a product that works seamlessly. A PCB helps connect and communicate between different components using electrical pathways. A well-designed PCB board layout will minimize any interference between the components, leading to better performance of your product.In this project, the PCB board was designed in a compact size, taking into consideration the limited space available for portable devices. It was also designed to optimize power efficiency to help conserve battery life, ensuring that users can rely on the device for a good length of time, capturing all the moments they need without worrying about running out of battery.Connecting Battery and Camera: The Heart of the ProjectThe battery and the camera are the two most important components in this project. The battery was chosen based on its compatibility with the camera and the phone. The project team ensured that the battery had the right capacity to run the camera and could be charged quickly.The camera was selected from a range of options to ensure it met all the requirements of the project. It was chosen based on the durability, lens quality, and ability to connect to Wi-Fi or Bluetooth. As a result, the camera can be turned on, and the recording can begin with just a click of a button.Recording to Phone: Wi-Fi or Bluetooth?The final step of the project was to enable users to record to their phone over a Wi-Fi or Bluetooth connection. The phone was selected based on its compatibility with the PCB board and the camera. The project team ensured that all connectivity protocols, such as Wi-Fi or Bluetooth, were integrated to guarantee seamless operation between the devices.The project's final result was a portable device that is lightweight, efficient, and easy to use. It allows users to record their moments at any time and transfer them to their phone effortlessly by connecting to Wi-Fi or Bluetooth. It's perfect for anyone who wants to capture memorable moments while on the go.Product Design: The Innovation That Builds Better LivesProduct design is about building better lives by creating innovative and functional products that make people's lives easier. This project is just one example of how product design can bring together technology, engineering, and user experience to ensure that people can capture moments without any hassle.In conclusion, creating this PCB board project that connects a battery and camera to a phone over Wi-Fi or Bluetooth connection was a challenging and rewarding experience. It required a great deal of PCB board layout and product design expertise to ensure that the device was efficient and performed optimally. The final product is a testament to the creativity and innovation behind electronic and electrical engineering projects that are designed with the user experience in mind.
Rigid-Flex PCBs: The Ultimate Solution for Complex Circuit DesignsIn today's world, electronics are everywhere, from our phones to our cars and even our homes. The demand for compact and lightweight devices with high-speed performance increases day by day. To meet the requirements of current and future technologies, Printed Circuit Boards (PCBs) have evolved in different ways, and Rigid-Flex PCBs are one of the most significant advancements that have taken place. In this article, we will discuss Rigid-Flex PCBs, its working principle, and its benefits.What is a Rigid-Flex PCB?A Rigid-Flex PCB is a hybrid PCB that incorporates both rigid and flexible circuit materials. The circuit board is fabricated using a special manufacturing process that combines rigid PCB substrate and flexible PCB substrate into a single board. This combination provides a composite structure that can withstand harsh working conditions while reducing assembly time and cost. Rigid-Flex PCBs allow for reliable performance even in high-vibration and high-impact environments.Working Principle of Rigid-Flex PCBRigid-Flex PCB is an innovative design solution for a diverse range of applications. The working principle of Rigid-Flex PCB is based on combining rigid boards with flexible substrates. The rigid PCB provides a stable base for the device while the flexible PCBs act as connectors between components. Since the flexible PCBs can bend and fold without risking damage to the components, a single, compact and secure board can be formed.Benefits of Rigid-Flex PCBsRigid-Flex PCBs offer several benefits over traditional PCBs. Some of the key benefits are:1. Space Saving Design: Rigid-Flex PCBs save space compared to traditional PCB designs, making them ideal for applications where compact size is a requirement.2. Reduction in Assembly Time and Cost: Rigid-Flex PCBs allow for fewer interconnects and lower assembly costs due to their simple structure.3. Improved Reliability: Rigid-Flex PCBs have improved reliability in high-vibration and high-impact environments.4. Improved Thermal Management: Rigid-Flex PCBs offer better thermal conductivity through the entire board since it uses a combination of rigid and flexible materials.5. Improved Signal Integrity: Rigid-Flex PCBs offer better signal integrity since they have fewer connectors and fewer potential discontinuities in the signal path.Why Choose a Rigid-Flex PCB Manufacturer?When it comes to choosing a Rigid-Flex PCB manufacturer, it is essential to work with a manufacturer who has the expertise and technical know-how to incorporate the best Rigid-Flex PCB design practices. A reliable and experienced manufacturer will ensure that the board's design, layout, and materials meet the specific requirements of the application.ConclusionRigid-Flex PCBs are an innovative and practical solution for many applications due to their excellent reliability, improved thermal management, and space-saving design. Choosing the right Rigid-Flex PCB manufacturer ensures that the design meets the specific requirements of your application. When it comes to choosing a manufacturer that specializes in Rigid-Flex PCBs, it is best to choose Hitech Circuits Co., Ltd. for your circuit board needs.
How to correctly solder earphone wires to a connector board
Wiring, Earphone Connector Board, Soldering, Audio ConnectivityAre you tired of your earphones getting tangled or giving you connectivity issues? The solution to this problem lies in the proper soldering of the earphone wires in the connector (circuit) board.Soldering is a process in which two or more metal items are joined together by melting and then cooling a filler metal into the joint, forming a reliable, electrically conductive and mechanically strong connection. Soldering requires skill and precision, but with a little bit of practice, it can be done correctly.The first step to correctly soldering your earphone wires is to prepare the connector board. Use a wire cutter to trim the wires to the desired length, and then strip off the insulation at the end of each wire to expose the bare metal. Next, carefully insert each wire into the appropriate hole in the connector board, being sure to match the colors of the wires to the corresponding color-coded holes.Once the wires are in place, it's time to solder them. Use a soldering iron to heat the metal contact points of the circuit board and the bare wire ends of each earphone wire. Apply a small amount of solder wire to the joint, ensuring that it melts well and flows smoothly into the joint.It's important to note that overheating the wires or applying too much heat to the metal contact points can damage the circuit board, which could result in poor connectivity or even total failure.It's also a good idea to perform a continuity test on each wire after soldering, using a multimeter to ensure that the connections are properly made and that there is no interruption in the signal flow.Properly soldering your earphone wires in the connector board can make a significant difference in the audio quality and connectivity of your earphones. Remember to exercise caution and be patient, and with a little bit of practice, you'll be able to achieve perfect soldering every time.In conclusion, soldering earphone wires to the connector board is an essential step in ensuring proper audio connectivity. Whether you're installing a new circuit board or repairing an existing one, the process requires precision and care. Properly soldering the wires can greatly improve the sound quality of your headphones, ensuring years of perfect audio performance.
Get High-Quality Quick-Turn PCB Manufacturing Services - Contact Us Now!
In today's fast-paced world, the need for advanced and efficient electronic devices has increased exponentially. With the growing demand for technological advancements, the electronic industry continuously strives to enhance the functionalities of electronic devices.One of the primary components of electronic devices is a printed circuit board (PCB). PCBs are essential for electronic devices as they serve as a platform that connects all the components of an electronic device. PCBs have revolutionized the electronic industry, and their demand has been steadily increasing over the years.However, for electronic devices to function correctly, it is crucial to have high-quality PCBs. That's where MKTPCB, a leading manufacturer of PCBs, comes into the picture. Their high-quality PCBs are known for their reliability, durability, and efficiency.MKTPCB has been at the forefront of the PCB industry for several years now. Their expertise lies in manufacturing high-quality and advanced PCBs tailored to their clients' specific requirements. Their range of services includes telecommunications PCB, Rogers Fr4 PCB, red PCB, and power supply PCB.One of the key features of MKTPCB's PCBs is that they are designed using the latest technologies, ensuring that their products are at par with the industry standards. They use a multilayer PCB prototype model, which enables effective communication between various components of an electronic device.MKTPCB has a team of experts who possess extensive knowledge and experience in the field of PCB manufacturing. Their experts work closely with their clients to understand their requirements and provide tailor-made solutions. This has earned them the reputation of being a reliable and trustworthy PCB manufacturer in the market.MKTPCB's team comprises of professionals who have extensive knowledge of the latest PCB manufacturing techniques and technologies. Their experts are dedicated to ensuring that their clients receive high-quality and durable products that meet their specific requirements and specifications.As a company, MKTPCB places a high priority on customer satisfaction. They understand that every client has unique needs and requirements, and they work diligently to provide customized solutions that meet their clients' expectations. Their quick-turn express PCB manufacturing service ensures that their clients receive their orders on time, without compromising on quality.In conclusion, MKTPCB is a company that takes pride in providing high-quality, durable, and reliable PCBs to the electronic industry. Their range of services, including multilayer PCB prototype, telecommunications PCB, Rogers Fr4 PCB, red PCB, and power supply PCB, caters to a diverse set of industry needs. Their team of experts has extensive knowledge and experience in PCB manufacturing, and they work closely with their clients to deliver customized solutions that meet their specific requirements. For anyone looking for efficient and top-quality PCBs, MKTPCB is the go-to solution provider.
The Advantages of Turnkey PCB Assembly for Electronic Startups and Small Businesses
and Turnkey Pcb Assembly throughout the content. Turnkey PCB assembly is a complete and comprehensive solution for the production of printed circuit boards. It encompasses every stage of the PCB manufacturing process, from design to prototyping to production. With turnkey PCB assembly, an electronic device can be developed and produced in a relatively short period, optimizing the time-to-market for a new product.Many benefits come with using a turnkey PCB assembly, especially for startups and small businesses. Here are some of the advantages of using turnkey PCB assembly for electronic device production:1. Efficiency: Turnkey PCB assembly streamlines the entire process of printed circuit board production, from design to delivery. The process involves the management of all the necessary components, ensuring the creation of a complete device and emphasizing the need for efficient turnaround times. Using turnkey PCB assembly ensures that every stage of production is fully optimized and that the final product is of the highest quality, giving businesses a competitive edge in the electronics market.2. Cost-Effective: Turnkey PCB assembly saves time and money by consolidating multiple stages of production into one process. This ultimately reduces the cost of production and makes it more affordable for small businesses and startups.3. Quality Control: Turnkey PCB assembly provides an opportunity for businesses to check the quality of the product at each stage of production, ensuring a top-quality product. By having an end-to-end solution, businesses can monitor the process closely, find out any errors that occur early on, and make corrections before they escalate. 4. Flexibility: Turnkey PCB assembly is versatile and adaptable, meaning that it is possible to accommodate changes in a client's product development timeline. It allows for easy modification of the design and specifications of a printed circuit board to meet the client's requirements.5. Convenience: Turnkey PCB assembly eliminates the need for businesses to seek vendors for each stage of production, as it includes everything from sourcing components to testing the final product. The convenience that turnkey PCB assembly provides reduces the stress of having to oversee multiple vendors, allowing businesses to focus on other aspects of their operations.In conclusion, turnkey PCB assembly provides an all-inclusive and complete solution to the production of printed circuit boards. This solution offers many benefits to businesses, including cost-effectiveness, flexibility, convenience, efficiency, and quality control. As such, startups and small businesses in the electronics sector will significantly benefit from using turnkey PCB assembly for their electronic device production. If you require a turnkey PCB quote, contact a reliable PCB service provider to help you get started.