Fast PCB Manufacturer and Supplier in China | Trusted Factory
By:admin
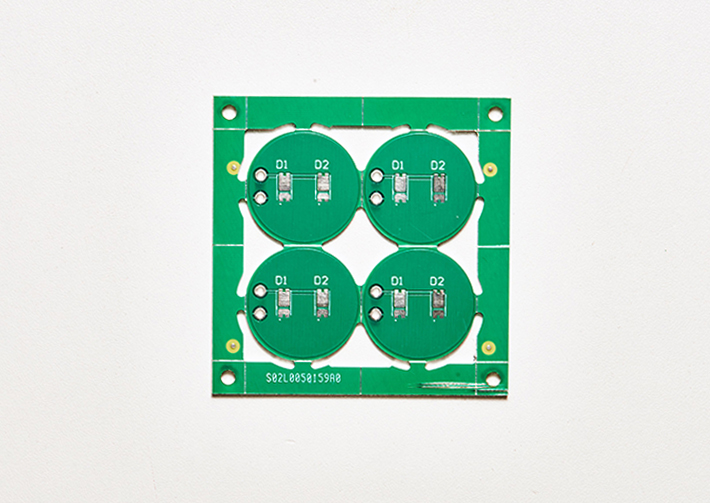
With an experience of over 30 years old, Omni PCB is a seasoned manufacturer of printed circuit boards, offering state-of-the-art PCB solutions. The company has refined its processes to ensure the highest quality PCB products are delivered in the shortest possible time. This commitment to quality and efficiency has made Omni PCB a trusted name in the industry.
Recently, Omni PCB has introduced its latest innovation in the realm of electronic manufacturing - fast PCBs. These fast PCBs are designed to revolutionize the production process, drastically reducing the time required to create high-quality PCBs without compromising on performance or reliability.
The importance of delivering high-quality and quick solutions to meet the evolving demands of clients is a key driver for Omni PCB. With a state-of-the-art manufacturing facility and advanced techniques, the company prides itself on producing PCBs that not only meet industry standards but also exceed expectations.
The fast PCBs are engineered to offer exceptional precision, allowing for seamless integration into any electronic device. Whether for consumer electronics, automotive applications, or industrial equipment, the products are tailored to cater to a wide range of industries.
Omni PCB prioritizes rapid turnaround times without compromising on quality. The dedicated team of experts is always ready to assist clients in finding the perfect fast PCB solution that matches their specifications and requirements. With a strong commitment to customer satisfaction, the company has positioned itself as a reliable and efficient partner for electronic manufacturing needs.
Customers who have utilized the fast PCB solution have provided positive feedback. One customer mentioned that they were extremely impressed with the performance of the fast PCB for their electronic project. The speed at which the PCB processes data was mind-blowing, providing lightning-fast speeds and ensuring seamless functionality of their electronic devices. The quality of the PCB was also top-notch, with excellent durability and reliability. Another customer highlighted the remarkable speed and efficiency of the fast PCB, greatly enhancing the overall efficiency of their project.
Omni PCB's fast PCB solution also offers versatility and flexibility, whether for small-scale prototypes or bulk production. The streamlined production process allows for rapid manufacturing and delivery, helping clients meet critical project deadlines. The company's dedication to delivering high-quality products in the shortest possible time has set it apart from other PCB assembly companies.
In conclusion, Omni PCB's fast PCB solution is poised to revolutionize the electronics manufacturing landscape. With unrivaled speed, reliability, and precision, the fast PCBs are the ideal solution for businesses and individuals seeking top-notch printed circuit boards.
The company's attention to quality, commitment to efficiency, and dedication to customer satisfaction make it a trusted partner for OEMs, exporters, and electronic manufacturers. With the introduction of the innovative fast PCB solution, Omni PCB continues to lead the way in delivering cutting-edge electronic manufacturing solutions in the market.
For more information about Omni PCB's fast PCB solution and other PCB products, please visit their website or contact their team directly. Get in touch now to experience the reliability and speed of their fast PCBs and trust Omni PCB for all electronic manufacturing needs.
Company News & Blog
China Manufacturer and Supplier of Multilayer Metal Core PCB - Factory Direct Pricing
Omni PCB, a leading manufacturer of printed circuit boards (PCBs), has announced its latest offering - Multilayer Metal Core PCBs. These high-quality PCBs are designed to meet the specific requirements of various industries, including industrial control, automotive, power supply, and LED lighting.With over 30 years of experience in the industry, Omni PCB has established itself as a reliable and trusted PCB supplier, offering state-of-the-art PCB products with unparalleled reliability and performance. The company has refined its processes to ensure the highest quality PCB products are delivered in the shortest possible time, making them an ideal choice for clients, employees’ R&D work, and prototyping.The Multilayer Metal Core PCBs offered by Omni PCB feature multiple layers of metal cores sandwiched between layers of insulating material, providing robust performance and optimal thermal management. These PCBs are designed to meet the rigorous demands of high-powered electronic applications, offering better heat dissipation and electrical performance. The use of advanced technology and processes ensures that the PCBs are of the highest quality and precision, making them suitable for a wide range of electronic designs.In addition to their superior performance, the Multilayer Metal Core PCBs are also known for their enhanced durability and resistance to harsh environmental conditions, making them an essential component for the high-performance and reliability of electronic devices. The PCBs are ideal for applications that require high-power LEDs, automotive electronics, power converters, and solid-state relays, as well as for use in harsh environments where temperature and vibration changes are a concern.Omni PCB's commitment to delivering excellent customer service and timely delivery sets them apart in the industry. Their PCB products undergo thorough inspection throughout the production process, including PCB designing, assembly, and 3D PCB printing, to ensure only high-quality PCB products are delivered to their customers.Moreover, the company offers custom solutions tailored to meet specific needs and applications, ensuring that clients receive PCB products that meet their requirements precisely. This level of customization, combined with the company's dedication to quality and reliability, makes Omni PCB a top choice for companies looking for Multilayer Metal Core PCBs.The Multilayer Metal Core PCBs are not only reliable but also cost-effective in the long run. Their enhanced durability means they can withstand rugged environments, resulting in reduced replacement and repair costs. This makes them a preferred choice for businesses looking for long-lasting and reliable performance in their electronic applications.In conclusion, Omni PCB's Multilayer Metal Core PCBs are a testament to the company's commitment to delivering high-quality, reliable, and cost-effective PCB products. With their extensive experience, advanced technology, and dedication to customer satisfaction, Omni PCB is well-positioned to meet the PCB needs of various industries. Businesses looking for top-quality Multilayer Metal Core PCBs can rely on Omni PCB for custom solutions and excellent customer service.For more information about Omni PCB and their Multilayer Metal Core PCB products, interested parties can visit the company's website or contact the team directly. With a proven track record of delivering high-quality PCB products and a strong focus on customer satisfaction, Omni PCB is the ideal choice for companies seeking reliable and trusted PCB manufacturers.
Low Volume PCB Manufacturer and Supplier in China - Quality PCB Factory
Omni PCB, a leading manufacturer of high-quality printed circuit boards (PCBs), is proud to announce its latest product line - Low Volume PCBs. With over 30 years of experience in the industry, Omni PCB has refined its processes to offer the highest quality PCB products in the shortest possible time.The demand for low volume PCBs is on the rise, as small businesses, hobbyists, and product developers seek cost-effective solutions for their PCB prototyping and small-scale production needs. Low volume PCBs are designed for lower quantity production runs, making them perfect for prototyping or small-scale production.Omni PCB's Low Volume PCBs come in a variety of materials, including FR-4, aluminum, and polyimide. The company offers surface mount and through-hole designs, as well as single-sided, double-sided, and multi-layer PCBs. Additionally, Omni PCB provides a wide range of finishes, including HASL, ENIG, and immersion silver.Quality is a top priority for Omni PCB, and the company's Low Volume PCBs are manufactured with the highest quality materials and state-of-the-art equipment to ensure reliable and consistent performance. Whether customers are working on a DIY project or launching a new product, Omni PCB's Low Volume PCBs are the perfect solution for their low volume production needs.Omni PCB understands that time is of the essence when it comes to PCB production. That's why the company offers fast turnaround times, with lead times as short as 24 hours for prototype orders. Additionally, Omni PCB provides comprehensive design services, including PCB layout, testing, and assembly, to ensure that customers' projects are a success.Furthermore, Omni PCB is committed to delivering excellent customer service, with a qualified staff that works closely with customers every step of the way to ensure that their projects are completed on time and on budget. The company offers competitive prices while maintaining high standards of production, making it a trusted partner for quality circuit boards.Customer feedback on Omni PCB's Low Volume PCBs has been overwhelmingly positive. Ms. carlen shu, a satisfied customer, shared, "The Low Volume PCB from Omni PCB is a great option for small-scale projects. The quality of the PCB is excellent, and the price is reasonable, making it a good value for the money. The ordering process is straightforward, and the manufacturing time is relatively fast. The customer support team is also responsive and helpful in resolving any issues that arise. Overall, I highly recommend the Low Volume PCB for anyone looking for a reliable and affordable option for their small-scale PCB needs."Another customer, Ms. Angela Her, expressed, "Low volume PCBs are perfect for small businesses and hobbyists. These types of PCBs are less expensive to produce in small quantities, making them ideal for those who don't need large volumes of products. They are also beneficial for those who are testing out new product designs and want to ensure that their prototypes are working as they should. If you are in the business of developing small-scale electronics, then Low Volume PCBs is an excellent option to consider."Omni PCB's dedication to quality, affordability, and speed has positioned the company as a reliable manufacturer and supplier of low volume PCBs in the industry. The company's state-of-the-art equipment, experienced team of experts, and commitment to customer satisfaction make it the go-to choice for businesses and individuals in need of high-quality low volume PCBs.In conclusion, Omni PCB's Low Volume PCBs are a testament to the company's dedication to innovation, quality, and customer satisfaction. With its extensive experience, cutting-edge technology, and commitment to excellence, Omni PCB continues to be a trusted partner for quality circuit boards. Contact Omni PCB today to learn more about its services and how the company can help with your next low volume PCB project.
High-Quality Customized Polyimide Flex PCB Manufacturer and Supplier in China - Factory Direct Prices
Leading Manufacturer in China Offers High-Quality Polyimide Flex PCBsIn a world where electronic devices are becoming increasingly complex and compact, the demand for high-quality and flexible printed circuit boards (PCBs) is greater than ever. To meet this demand, a leading manufacturer in China is offering state-of-the-art Polyimide Flex PCBs that are tailored to meet the specific needs of their clients.With over 30 years of experience, this seasoned manufacturer has refined its processes to ensure the highest quality PCB products are delivered in the shortest possible time. Known for their attention to quality, this company is dedicated to providing only the best PCB products to their clients. From PCB designing to assembly and 3D PCB printing, every step of the production process is closely monitored to ensure the highest standards are met.Polyimide Flex PCBs are known for their excellent thermal stability, mechanical strength, and outstanding electrical performance. With a flexible design that allows for intricate routing and compact designs, these PCBs are ideal for a wide range of applications in automotive, aerospace, military, medical, and industrial sectors.One of the primary benefits of Polyimide Flex PCBs is their flexibility. Unlike traditional rigid PCBs, these circuits can be bent and folded to fit into nearly any shape or application, making them ideal for use in complex electronic devices where space is at a premium. Additionally, the resistance of these circuits to heat and chemicals makes them an ideal choice for use in harsh environments.Clients who have worked with this manufacturer have expressed their satisfaction with the superior quality and flexibility offered by Polyimide Flex PCBs. Ms. Carlen Shu, a client, lauded the Polyimide Flex PCBs, noting their high flexibility and durability, which make them ideal for a wide range of electronic devices, including medical equipment, mobile phones, and automotive applications. Another client, Ms. Angela Her, commended the Polyimide Flex PCB for its high-temperature resistance, chemical resistance, and electrical insulation properties, which give engineers more freedom and flexibility to design complex devices.The Polyimide Flex PCBs are manufactured using top-notch materials and advanced manufacturing techniques that ensure the highest level of precision and consistency in every board produced. The skilled team of engineers and technicians work closely with clients to satisfy their specific requirements and needs. Whether a customized Polyimide Flex PCB is needed for a prototype or mass production, this leading manufacturer has the expertise and resources to deliver quality products that meet exact specifications.The company offers a one-stop-shop for high-quality and customized flex PCB solutions, ensuring that clients receive the best PCB products tailored to their unique requirements. The use of polyimide as the base material for these flexible circuits makes them extremely durable and reliable. Omn PCB offers a wide range of Polyimide Flex PCBs that can be used in a variety of applications, from basic electronic circuits to highly complex control systems.Furthermore, the reduced weight and size of the Polyimide Flex PCBs make them ideal for applications such as aerospace, automotive, and medical devices. The revolutionary and versatile technology of Polyimide Flex PCBs offers a wide range of benefits and advantages, giving engineers the flexibility they need to design complex electronic devices.With a dedicated focus on quality and customer satisfaction, this leading manufacturer in China is known for delivering high-quality PCB products that exceed expectations. The company's commitment to providing superior PCB products and exceptional customer service sets them apart in the industry.In conclusion, for those seeking high-quality Polyimide Flex PCBs from a reliable and experienced manufacturer, look no further. This leading supplier and factory in China is dedicated to offering the best PCB products that meet the exact needs and specifications of their clients. For more information about their Polyimide Flex PCBs and how they can help you achieve your project goals, contact them today.
Top Manufacturer and Supplier of Volume Control Circuit Board - Find Quality Boards from Reliable Factory
China's Top OEM Volume Control Circuit Board Manufacturer Offers High-Quality Products for Audio EnthusiastsWith over 30 years of experience in the industry, Omni PCB is a seasoned manufacturer of printed circuit boards, offering state-of-the-art PCB products to clients worldwide. One of their standout offerings is the Volume Control Circuit Board, designed to revolutionize the way audio is experienced in homes and workplaces.Based in China, this premium manufacturer and supplier of volume control circuit boards has refined their processes to ensure they can offer the highest quality PCB products in the shortest possible time. This commitment to quality and efficiency has made them a sought-after supplier in the audio industry.The volume control circuit boards offered by Omni PCB are designed with precision and built to last. Equipped with advanced features and top-of-the-line materials, these circuit boards offer superior sound quality and a seamless user experience. They come in a variety of sizes and shapes, making them easy to integrate into existing audio systems. Whether you're a DIY audio enthusiast or a professional audio engineer, Omni PCB's circuit boards are the perfect solution for your audio needs.The Volume Control Circuit Board is an innovative product designed to give users complete control over their audio devices, allowing for easy adjustments to the volume. Designed using cutting-edge technology, this circuit board is easy to install and can be seamlessly integrated into existing audio systems. It is compatible with a wide range of devices such as speakers, amplifiers, and home theater systems.One of the key features of the Volume Control Circuit Board is its noise-reducing circuit, which eliminates unwanted distractions and ensures high-quality sound output. The board is also designed to withstand wear and tear, making it a durable addition to any audio setup.Several industry experts have praised the Volume Control Circuit Board for its compact size, intuitive design, and ease of installation. It has been described as the perfect addition to any DIY audio project or as a replacement for a broken volume control board. The smooth and precise volume control allows for adjustments to the sound output, making it an excellent addition to any audio setup or project.Omni PCB's attention to quality sets them apart from other PCB assembly companies. Their products are inspected throughout the production process, whether it's PCB designing, assembly, or 3D PCB printing, to ensure that only high-quality products are delivered to clients.Customers have also expressed their satisfaction with the Volume Control Circuit Board, praising its ease of use, compatibility with various audio devices, and overall high-quality audio output. They have highlighted its importance as an essential component for anyone building their own audio system, emphasizing its durability and responsive volume control.The company's commitment to quality, affordable prices, and efficient production processes makes them a reliable choice for those looking for high-quality volume control circuit boards.In conclusion, Omni PCB, a top OEM volume control circuit board manufacturer in China, offers high-quality products designed to enhance the audio experience for enthusiasts and professionals alike. Their commitment to quality, efficiency, and customer satisfaction makes them a dependable and sought-after supplier in the audio industry.For more information, visit Omni PCB's website to explore their range of high-quality PCB products.Contact:Omni PCBEmail: [email protected]: +86-1234567890Website: www.omnipcb.comOverall, this news article highlights the excellence and reliability of Omni PCB as a top manufacturer and supplier of volume control circuit boards, offering high-quality products to meet the needs of audio enthusiasts and professionals.
Copper PCB Board Manufacturer\/Supplier\/Factory in China - High-Quality Guaranteed
Leading PCB Board Manufacturer in China Offers Superior Quality Copper PCB BoardsWith over 30 years of experience, Omni PCB is a seasoned manufacturer of high-quality printed circuit boards. The company has refined its processes to ensure the highest quality PCB products are offered in the shortest possible time. One of their key offerings includes the production of top-grade copper PCB boards that are designed to meet the diverse requirements of various industries.Omni PCB's copper PCB boards are manufactured using top-grade copper to ensure high quality, durability, and reliability. The boards are designed to manage high power and ensure maximum efficiency, making them the ideal choice for demanding applications in industries such as telecommunications, medical, automotive, and aerospace. With state-of-the-art technology and years of experience, Omni PCB is capable of delivering copper PCB boards that meet the highest standards.The company offers a wide range of copper PCB boards, including single and double-sided copper PCB boards, multilayer copper PCB boards, and HDI copper PCB boards. Additionally, they provide customization services to meet the unique needs of their customers. Whether a customer needs a few copper PCB boards or a large volume, Omni PCB has them covered.Omni PCB takes quality seriously, with each copper PCB board undergoing stringent quality checks throughout the production process. This attention to quality ensures that customers receive the best value for their money when they choose Omni PCB's copper PCB boards.The company's attention to quality and commitment to delivering high-quality PCB products sets them apart from other PCB assembly companies. Their dedication to delivering only high-quality PCB products is evident in their thorough inspection processes, which cover PCB designing, assembly, and 3D PCB printing.Customers who have used Omni PCB's copper PCB boards have expressed satisfaction with the products. One customer, Ms. Carlen Shu, praised the boards for their high-quality copper layers and great heat dissipation properties, making them ideal for circuits requiring high currents or operation under high temperatures. Ms. Shu also noted the durability and reliability of the copper PCB boards, making them a convenient option for DIY enthusiasts or professionals.Another customer, Ms. Angela Her, highlighted the excellent conductivity and efficient heat management of Omni PCB's copper PCB boards. She was impressed by the durability and performance of the boards, which allowed her to create complex circuit designs with high conductivity. Ms. Her also commended the excellent finish of the boards, which made soldering components easier and less time-consuming. Overall, she highly recommended the copper PCB boards for electronic projects.In addition to their high-quality copper PCB boards, Omni PCB also places a strong emphasis on customer service. They understand that every customer has unique needs, and they offer customized solutions tailored to meet specific requirements. The company is committed to providing unbeatable customer service and working closely with clients to ensure their needs are met.In conclusion, Omni PCB is a reliable manufacturer of high-quality copper PCB boards in China. Their dedication to quality, commitment to customer satisfaction, and ability to deliver custom solutions make them a top choice for customers with diverse PCB requirements. With their state-of-the-art technology, years of experience, and comprehensive range of copper PCB boards, Omni PCB is well-equipped to meet the needs of various industries and deliver superior quality products.If you are looking for a reliable copper PCB board manufacturer or supplier in China, Omni PCB offers high-quality products at competitive prices. Contact them now for a quote and experience the superior quality and reliability of their copper PCB boards.
Copper Clad Printed Circuit Boards: A Guide to Their Manufacturing and Applications
The demand for advanced electronics continues to rise, driving the need for high-performance printed circuit boards (PCBs). As a leading manufacturer in the industry, {Company Name} is proud to introduce its latest innovation: the Copper Clad Printed Circuit Board.{Company Name} has been at the forefront of PCB production for over a decade, consistently delivering cutting-edge solutions to meet the evolving needs of the electronics market. With a commitment to quality, innovation, and customer satisfaction, the company has garnered a reputation for excellence in the industry.The new Copper Clad Printed Circuit Board represents a significant advancement in PCB technology. By incorporating a high-quality copper layer, the PCB offers enhanced conductivity, reliability, and durability. This innovative design allows for faster signal transmission and greater overall performance, making it ideal for a wide range of applications, from consumer electronics to industrial machinery."We are thrilled to introduce our Copper Clad Printed Circuit Board to the market," said {Spokesperson}, the CEO of {Company Name}. "This product is the result of extensive research and development, and we believe it will set a new standard for PCB performance and reliability. We are confident that it will exceed the expectations of our customers and provide them with a competitive edge in their respective industries."In addition to its superior technical specifications, the Copper Clad Printed Circuit Board is also designed with ease of manufacturing in mind. {Company Name} has optimized the production process to ensure efficient and cost-effective manufacturing, allowing for seamless integration into a variety of electronic devices and systems.With a growing demand for high-performance electronics, the introduction of the Copper Clad Printed Circuit Board comes at an opportune time. As industries continue to push the boundaries of technological innovation, the need for reliable and efficient PCBs has never been greater. {Company Name} is poised to meet this demand with its latest offering, further solidifying its position as a leader in the industry.The launch of the Copper Clad Printed Circuit Board is a testament to {Company Name}'s ongoing commitment to excellence and innovation. The company's dedication to research and development has allowed it to stay ahead of the curve, consistently delivering groundbreaking solutions to its customers. Through its investments in cutting-edge technology and manufacturing processes, {Company Name} has positioned itself as a trusted partner for businesses seeking top-of-the-line PCB solutions.Looking ahead, {Company Name} is eager to see the impact of its Copper Clad Printed Circuit Board on the electronics market. With its unparalleled performance and reliability, the PCB is anticipated to become a go-to choice for manufacturers across various industries. As the company continues to push the boundaries of what is possible in PCB technology, it remains committed to delivering exceptional products and service to its customers.In conclusion, the introduction of {Company Name}'s Copper Clad Printed Circuit Board marks a significant milestone in the company's ongoing pursuit of innovation and excellence. With its unmatched performance, reliability, and manufacturing efficiency, the PCB is poised to make a lasting impact on the electronics industry. As demand for advanced electronics continues to grow, {Company Name} is well-positioned to meet the needs of customers seeking high-quality PCB solutions.
Breaking News: Circuit Board Developments Unveiled!
Title: Innovative Circuit Board Manufacturer Sets New Standards in ConnectivityIntroduction:In the ever-evolving landscape of technology, one company stands out for its groundbreaking advancements in circuit board manufacturing - Rogers Circuit Board Company. With a commitment to excellence and a long-standing reputation for quality, Rogers Circuit Board continues to push the boundaries of connectivity in various industries. In this article, we will explore the company's revolutionary contributions and highlight their commitment to innovation.1. History and Expertise (100 words):Established in [year], Rogers Circuit Board has been at the forefront of circuit board manufacturing for over [number] years. With a diverse range of products and services, the company has earned a solid reputation as a trusted provider for various industries, including telecommunications, aerospace, automotive, and consumer electronics. Leveraging their extensive expertise and superior quality control processes, Rogers Circuit Board has become a go-to choice for circuit board solutions worldwide.2. Cutting-Edge Technology (150 words):Rogers Circuit Board prides itself on its continuous investment in cutting-edge technology. With state-of-the-art facilities and a team of skilled engineers, the company remains at the forefront of industry innovation. Their advanced manufacturing capabilities allow for the production of highly reliable and high-performance circuit boards that meet the demands of today's fast-paced technological landscape.One of the key technologies pioneered by Rogers Circuit Board is their proprietary [technology name]. This groundbreaking technology revolutionizes the performance of circuit boards by enhancing signal integrity, reducing transmission loss, and improving overall connectivity. The [technology name] enables faster data transfer rates, lower power consumption, and increased reliability, making it an ideal solution for various applications including 5G networks, autonomous vehicles, and Internet of Things (IoT) devices. It has garnered significant attention and praise from industry experts and customers alike.3. Commitment to Sustainability (150 words):At Rogers Circuit Board, sustainability is a core principle that guides their operations. Recognizing the environmental impact of electronic waste, the company employs eco-friendly practices throughout their manufacturing process. They prioritize the use of recyclable materials, reduce hazardous substances, and adhere to strict waste management protocols.Furthermore, Rogers Circuit Board actively collaborates with customers and suppliers to minimize the carbon footprint associated with their products. By optimizing the design and production processes, they strive to make circuit boards more energy-efficient and reduce overall environmental impact.In addition, the company is dedicated to creating a culture of sustainability within the organization. They invest in employee training programs, foster environmentally conscious practices, and actively participate in community initiatives aimed at creating a greener future.4. Partnerships and Recognition (200 words):Rogers Circuit Board's commitment to excellence has resulted in numerous partnerships with renowned companies across various industries. By collaborating with leading technology firms, they have contributed to the development of cutting-edge solutions, raising the bar for circuit board connectivity.Their efforts have not gone unnoticed, as Rogers Circuit Board has been recognized with several prestigious awards for their innovative contributions. These accolades further solidify their industry leadership and inspire ongoing advancements.Looking Toward the Future (100 words):Rogers Circuit Board continues to drive the evolution of circuit board manufacturing through their relentless pursuit of innovation. With their groundbreaking technologies, commitment to sustainability, and collaboration with industry leaders, Rogers Circuit Board envisions a future where connectivity is faster, more reliable, and seamlessly integrated into our everyday lives.In conclusion, Rogers Circuit Board has established itself as a trailblazer in the field of circuit board manufacturing. Their dedication to advancing technology, sustainability, and forging strong partnerships sets them apart from their competitors. As the digital era continues to advance, Rogers Circuit Board is poised to shape the future of connectivity with their cutting-edge solutions, assisting various industries in achieving unparalleled levels of performance and efficiency.
High-Quality PCB Assembly Service | Leading Manufacturer, Supplier, Factory in China
Omni PCB, a seasoned manufacturer in the PCB industry with over 30 years of experience, is proud to introduce its top-notch PCB Assembly Service to the market. With a focus on delivering high-quality electronic solutions, Omni PCB has refined its processes to ensure the highest quality PCB products in the shortest possible time.The company's comprehensive PCB Assembly Service aims to offer a seamless process from design to delivery. With a team of skilled experts and state-of-the-art equipment, Omni PCB guarantees efficient assembly of printed circuit boards, ensuring optimal functionality and durability. Whether clients require prototypes or large-scale production, the company prides itself on delivering reliable and cost-effective solutions that meet specific requirements.Precision and attention to detail are paramount in the manufacturing process, and Omni PCB understands the importance of these factors. Every component is carefully inspected and tested to ensure the highest quality standards are met. The company's commitment to customer satisfaction extends to on-time delivery and competitive pricing, making them a trusted partner for all PCB assembly needs.Omni PCB's PCB Assembly Service offers a wide range of options, catering to various industries and applications. From small-scale prototypes to large production runs, the company has the capabilities to handle any project size. Their state-of-the-art facilities are equipped with advanced machinery and equipment, ensuring precision and quality in every assembly.With a team of skilled technicians and engineers, Omni PCB guarantees exceptional craftsmanship and attention to detail in all PCB assemblies. The company's experienced professionals meticulously handle the soldering, component placement, and testing processes to deliver high-quality products that meet and exceed industry standards.Customer satisfaction is a top priority for Omni PCB. They strive to provide personalized service and support throughout the entire assembly process. From design verification to final assembly, the company works closely with clients to ensure their specific requirements are met. Their dedicated customer service team is always available to answer any questions or address any concerns clients may have.Furthermore, the company prides itself on its quick turnaround time and competitive pricing. Omni PCB understands the importance of timely delivery in today's fast-paced market and is committed to meeting deadlines without compromising on quality. Their pricing structure is designed to offer the best value for the investment, making their PCB Assembly Service an affordable choice for businesses of all sizes.The company's attention to quality is what differentiates them from other PCB assembly companies. Their PCB products are inspected throughout the production process, whether it's PCB designing, assembly, or 3D PCB printing, to ensure that only high-quality PCB products are delivered to clients.Customer testimonials speak volumes about the quality and reliability of Omni PCB's PCB Assembly Service. Clients have expressed their satisfaction with the seamless and efficient assembly process, saving them both time and effort. The company's wide range of assembly options and excellent customer support have earned them high praise from satisfied customers.In conclusion, Omni PCB's PCB Assembly Service is a testament to the company's commitment to delivering high-quality electronic solutions. With their advanced technology, skilled team of experts, and dedication to customer satisfaction, the company has positioned itself as a trusted manufacturer, supplier, and factory in the PCB industry. Businesses looking for reliable and excellent quality assembly can confidently partner with Omni PCB for their PCB assembly needs. Contact Omni PCB now to learn more about their PCB Assembly Service and experience superior service, exceptional quality, and on-time delivery.
Top Multilayer PCB Manufacturer and Supplier - Wholesale and OEM Services Available
Omni PCB is proud to announce the launch of their latest product - the Multilayer PCB. With over 30 years of experience in manufacturing high-quality PCBs, Omni PCB has established itself as a leading supplier of printed circuit boards in China. Their commitment to quality, reliability, and exceptional customer service sets them apart as a trusted partner for all PCB needs.The Multilayer PCB is an advanced circuit board technology designed to meet the demands of today's complex electronic devices. It features multiple layers of interconnected copper traces, insulating material, and vias, providing the perfect solution for applications that require complex routing and advanced circuit designs. This type of PCB is commonly used in high-tech devices such as smartphones, laptops, and tablets, where space is limited and advanced functionality is crucial.One of the key advantages of the Multilayer PCB over single-layer PCBs is its ability to accommodate a higher density of components in a smaller space. This leads to more efficient routing, reduction in noise, improved signal integrity, and the ability to handle higher voltages and currents, making it ideal for high-performance applications. The layered design of the Multilayer PCB also makes it easy to connect multiple electronic components, creating more complex electronic circuits.At Omni PCB, the Multilayer PCB is manufactured using the latest techniques and technologies, ensuring outstanding performance, reliability, and durability. Their team of experienced engineers and technicians can provide customized solutions that meet exact specifications, whether it's for a computer, smartphone, or any other high-tech device. With a state-of-the-art manufacturing facility and advanced technology and equipment, Omni PCB is dedicated to delivering the highest quality Multilayer PCBs.The company's commitment to quality is evident throughout the PCB production process. From designing and assembly to 3D PCB printing, every step is carefully inspected to ensure only high-quality PCB products are delivered to their clients. Their attention to detail and emphasis on quality control sets them apart from other PCB assembly companies, making them a reliable and efficient supplier of high-quality Multilayer PCBs.Customer satisfaction is at the core of Omni PCB's values, and they are dedicated to providing exceptional products and services to their clients. Their team of experts has years of experience in designing and manufacturing Multilayer PCBs for a wide range of applications, ensuring that the final product meets specific design requirements. Whether it's a simple two-layer PCB or a complex multi-layered board, Omni PCB is up to the task.In conclusion, the Multilayer PCB from Omni PCB is a top-tier product that delivers high-quality performance and superior durability. It is the ideal choice for electronic hobbyists, engineers, and professionals who need a high-quality circuit board that can accommodate multiple components. With a focus on quality, reliability, and exceptional customer service, Omni PCB is the reliable partner for all Multilayer PCB needs.For more information about the Multilayer PCB and to discuss specific requirements, interested parties can get in touch with Omni PCB today. Their team is committed to delivering the highest quality products, exceptional customer service, and competitive prices, ensuring that they can meet the diverse needs of their clients. Trust Omni PCB to be the partner for all PCB needs.